Курс, группа 3,1 фаткуллин руслан айратович работа на тему: расчет и выбор посадок гладких цилиндрических и типовых соединений, расчет размерной цепи
СОДЕРЖАНИЕ: Расчет и выбор посадок гладких цилиндрических и типовых соединений, расчет размерной цепиМИНИСТЕРСТВО СЕЛЬСКОГО ХОЗЯЙСТВА РОССИЙСКОЙ ФЕДЕРАЦИИ
БАШКИРСКИЙ ГОСУДАРСТВЕННЫЙ АГРАРНЫЙ УНИВЕРСИТЕТ
Факультет Механизации сельского хозяйства
Кафедра ТМ и РМ
Специальность Автомобили и А/Х
Форма обучения Очная
Курс, группа 3,1
ФАТКУЛЛИН РУСЛАН АЙРАТОВИЧ
Курсовая работа
на тему: РАСЧЕТ И ВЫБОР ПОСАДОК ГЛАДКИХ ЦИЛИНДРИЧЕСКИХ И ТИПОВЫХ СОЕДИНЕНИЙ, РАСЧЕТ РАЗМЕРНОЙ ЦЕПИ
«К защите допускаю»
Руководитель:
__Рафиков И.А___
(Ученая степень, звание, Ф.И.О.)
______________________________
(подпись)
«___» _____________ 2009 г.
Оценка при защите
___________________________
___________________________
(подпись)
«___» ____________ 2009 г.
Уфа 2009
РЕФЕРАТ
Работа: 27 листов., 9 рисунков, 4 таблиц, библиографический список включает 8 источников.
РАСЧЕТ И ВЫБОР ПОСАДОК ГЛАДКИХ ЦИЛИНДРИЧЕСКИХ И ТИПОВЫХ СОЕДИНЕНИЙ, РАСЧЕТ РАЗМЕРНОЙ ЦЕПИ
Отметим, что вал и отверстие, образующие посадку, имеют один и тот же номинальный размер и различаются верхними и нижними отклонениями. По этой причине на чертежах над размерной линией, посадку обозначают после номинального размера дробью, в числители которой записывают предельные отклонения для отверстия, а в знаменателе – аналогичные данные для вала.
Разность размеров вала и отверстия до сборки, если размер вала больше размера отверстия, называется натягом N . Посадка с натягом – это посадка, при которой обеспечивается натяг в соединении, а поле допуска отверстия расположено под полем допуска вала.
Наименьший N min и наибольший N max натяги имеют важные значения для посадки с натягом:
N min имеет место в соединении, если в отверстии с наибольшим предельным размером D max будет запрессован вал наименьшего предельного размера d min ;
N max имеет место при наименьшим предельном размере отверстия D min и наибольшим предельном размере вала d max .
S min имеет место в соединении отверстия с валом образуется, если в отверстии с наименьшим предельным размером D min , будет установлен вал с наибольшим предельным размером d max;
S max имеет место при наибольшем предельном размере отверстия D max и наименьшим предельном размере вала d min .
Разность между наибольшим наименьшим зазорами или сумма допусков отверстия и вала, составляющих соединения, называются допуском посадки.
ВВЕДЕНИЕ
Допуски размеров, посадки и допуски посадок.
Начнем с того, точность изготовления детали характеризует допуск. И чем он меньше, тем труднее обрабатывать деталь. Это происходит из-за повышения требований к точности станка, инструмента, приспособлений, квалификации рабочего. Важно знать, что неоправданно больший допуск снижает надежность и качество работы изделия.
Полем допуска называют поле, ограниченное верхним и нижним отклонениями. Поле допуска определяется величиной допуска и его положением относительно номинального размера. При графическом же изображении оно заключают между линиями, соответствующими верхнему и нижнему отклонениям нулевой линии.
При нанесении на чертежи размеров с верхним и нижним отклонением следует соблюдать определенные правила:
- верхнее или нижнее отклонения, равные нулю, не указываются.
- количество знаков в верхним и нижнем отклонениях выравнивают, при необходимости для сохранения одинокого числа знаков справа дописывают нули, например .
- верхнее и нижнее отклонения записывают в две строки, причем верхнее отклонение располагают над нижним; высота цифр отклонения примерно вдвое меньше цифр номинального размера;
- в случае симметричного расположения поля допуска относительно нулевой линии, т.е. когда верхнее отклонение равно по абсолютной величине нижнему отклонению, но противоположно по знаку, их значение указывают после знака ± цифрами, равными по высоте цифрам номинального размера;
Поле допуска характеризует не только величину допуска, но и расположение его относительно номинального размера или нулевой линии. Оно может быть расположено выше, ниже, симметрично, односторонне и асимметрично относительно нулевой линии. Для наглядности на чертежах деталей над размерной линией после номинального размера принято указывать верхнее и нижнее отклонение в миллиметрах с их знакам, а также для наглядности строят схемы расположения поля допуска вала или отверстия относительно нулевой линии; при этом верхние и нижние отклонения откладывают в микрометрах, а не в миллиметрах.
Посадка - характер соединения детали, определяемый величиной получающихся в нем зазоров или натягов. Различают посадки трех тиков:
- с зазором;
- с натягом ;
- переходные.
Отметим, что вал и отверстие, образующие посадку, имеют один и тот же номинальный размер и различаются верхними и нижними отклонениями. По этой причине на чертежах над размерной линией, посадку обозначают после номинального размера дробью, в числители которой записывают предельные отклонения для отверстия, а в знаменателе – аналогичные данные для вала.
Разность размеров вала и отверстия до сборки, если размер вала больше размера отверстия, называется натягом N . Посадка с натягом – это посадка, при которой обеспечивается натяг в соединении, а поле допуска отверстия расположено под полем допуска вала.
Наименьший N min и наибольший N max натяги имеют важные значения для посадки с натягом:
N min имеет место в соединении, если в отверстии с наибольшим предельным размером D max будет запрессован вал наименьшего предельного размера d min ;
N max имеет место при наименьшим предельном размере отверстия D min и наибольшим предельном размере вала d max .
Разность размеров отверстия и вала до сборки, если размер отверстия больше отверстия вала, называют зазором S . Посадка, при которой обеспечивается зазор в соединении и поле допуска отверстия расположено над полем допуска вала, называют посадкой с зазором. Ее характеризует наименьший S min и наибольший S max зазоры:
S min имеет место в соединении отверстия с валом образуется, если в отверстии с наименьшим предельным размером D min , будет установлен вал с наибольшим предельным размером d max;
S max имеет место при наибольшем предельном размере отверстия D max и наименьшим предельном размере вала d min .
Разность между наибольшим наименьшим зазорами или сумма допусков отверстия и вала, составляющих соединения, называются допуском посадки .
А посадка, при которой возможно получение, как зазора, так и натяга, называют переходной посадкой . В данном случае поля допусков отверстия и вала перекрываются частично или полностью.
Вследствие неизбежного колебания размеров вала и отверстия от наибольшего до наименьшего значений, при сборке деталей, возникает колебание зазоров и натягов. Наибольшие и наименьшие зазоры, а также натяги рассчитываются по формулам. И чем меньше колебание зазоров или натягов, тем выше точность посадки.
ОГЛАВЛЕНИЕ
ВВЕДЕНИЕ
2 АНАЛИЗ ПОСАДКИ………………………………………………………
2.1 Расшифровка условного обозначения посадки……………….
2.2 Определение среднего коэффициента точности………………
2.3 Определяем значение шероховатости………………………….
2.4 Определяем значения технологических зазоров………………
2.5 Определяем значения допусков и строим схему
полей допусков…………………………………………………….
2.6 Характеристика посадки
2.7 Расчетные характеристики посадки. Предельные
размеры……………………………………………………………..
2.8 Определение видов окончательной обработки и выбор
средств измерения деталей ………………………………………
2.9 Выполнение эскизов деталей соединения и узла в сборе……..
3 ПОСАДКИ ПОДШИПНИКОВ КАЧЕНИЯ…………………………….
3.1 Обоснование характера работы подшипника…………………
3.2 Расчет и выбор стандартного подшипника…………………….
3.3 Выбор посадок колец подшипника………………………………
3.4 Расчет посадки подшипника………………………………………
4 ВЫБОР ПОСАДКИ ПО АНАЛОГИИ……………………………………
5 ПОСАДКИ ШПОНОЧНОГО СОЕДИНЕНИЯ………………………….
5.1 Определение размеров шпоночного соединения……………….
5.2 Выбор полей допусков сопрягаемых размеров…………………
5.3 Эскизы шпоночного соединения и сопрягаемых деталей…….
6 РАСЧЕТ РАЗМЕРНОЙ ЦЕПИ……………………………………………
6.1 Составление размерной цепи ……………………………………..
6.2 Определение размеров звеньев ……………………………………
6.3 Расчет размерной цепи на максимум, минимум………………..
6.4 Расчет размерной цепи вероятностным методом………………
ЗАКЛЮЧЕНИЕ
БИБЛИОГРАФИЧЕСКИЙ СПИСОК
2 АНАЛИЗ ПОСАДКИ
Анализ посадки включает определение принадлежности ее к той или иной системе посадок, расчет характеристик соединения, назначение способов обработки деталей и их контроля.
При анализе конструкции узлов машин могут встретиться посадки, выполняемые как по единой системе допусков и посадок (ЕСДП), так и по системе ОСТ (часто встречающиеся в ремонтной (практике) внесистемные (специальные) посадки, а для импортной техники характерно применение Международной системы допусков (ИСО)).
Посадки следует анализировать в системе ЕСДП, а если числовые значения и расположение полей допусков отличаются от табличных приведенных в ГОСТ 25347 - 86, то их следует заменить близкими по значению полями допусков или посадками из системы ЕСДП /2/.
2.1 Расшифровка условного обозначения посадки
Посадка задана размером и числовыми значениями максимального и минимальго натяга:
36, Nmax P = 52 мкм, Nmin P = 21 мкм, cH. (1)
где 36- номинальный размер соединения;
Nmax P – натяг максимальный, мкм;
Nmin P – натяг минимальный, мкм.
2.2 Определение среднего коэффициента точности:
TS = Nmax P - Nmin P = 52 – 21 = 31 мкм. (2)
аср
= (3)
Принимаем ближайшее значение 7i (таблица 3):
Принимаем JT5.
Смотрим по таблице 1 значение стандартного допуска для данного квалитета:
Td = TD = 0,009.
2.3 Определяем значение шероховатости:
RzD = Rzd = 0,125 x TD = 0,125 x 9 = 1,125 мкм
Определяем стандартное значение шероховатости и принимаем:
RzD = Rzd = 1,25 мкм; (таблица 3 /4/)
2.4 Определяем значения технологических зазоров:
Nmax T = Nmax P + 1.4 (RzD + Rzd )= 52 – 1.4 (1.25 +1.25)= 55.5 мкм;
(4)
Nmin T = Nmin P + 1.4 (RzD + Rzd )=24.5 мкм.
2.5 Определяем значения допусков и строим схему полей допусков:
Предельные отклонения: ЕS = +11 мкм; ЕJ = + 0; (таблица 4/4/)
еs = +54 мкм; еi = +43 мкм.
В условном масштабе строится схема полей допусков (рисунок 2.1)
![]() |
Рисунок 2.1 Схема полей допусков посадки
2.6 Характеристика посадки
Посадка в системе отверстия, т. к. поле допуска отверстия основное с нижним отклонением равным нулю.
Посадка с натягом, т.к. поле допуска вала на схеме расположено выше поля допуска отверстия и размеры вала больше размеров отверстия до сборки.
2.7 Расчетные характеристики посадки. Предельные размеры:
- наибольший диаметр отверстия:
(5)
- наименьший диаметр отверстия:
(6)
- наибольший диаметр вала:
(7)
- наименьший диаметр вала:
(8)
Предельные и средние натяги:
- наибольший натяг:
мм; (9)
- наименьший натяг:
мм. (10)
Проверка:
мм;
мм. (11)
Средний натяг:
мм. (12)
Допуск посадки:
мм. (13)
Проверка:
мм. (14)
Выводы: Совпадение значений натягов и допуска посадки с проверочными, свидетельствует о верности расчетов.
Расчётные характеристики посадки сведем в таблицу 2.1.
Таблица 2.1 Сводные данные по расчёту характеристик посадки
Наименование параметров |
Обозначение |
Величина |
||
Отверстие |
Отклонение, мкм |
Верхнее |
|
+11 |
Нижнее |
|
0 |
||
Основное |
|
Нижнее |
||
Предельные размеры, мкм. |
Наибольший |
|
71,011 |
|
Наименьший |
|
71,0 |
||
Допуск, мкм. |
|
11 |
||
Вал |
Отклонения, мкм. |
Верхнее |
|
+54 |
Нижнее |
|
+43 |
||
Основное |
n |
Нижнее |
||
Предельные размеры, мкм. |
Наибольший |
|
70,054 |
|
Наименьший |
|
70,043 |
||
Допуск, мкм. |
|
11 |
||
Посадка |
Номинальный размер |
|
36 |
|
Предельные натяги, мкм. |
Наибольший |
|
54 |
|
Наименьший |
|
32 |
||
Средний |
|
43 |
2.8 Определение видов окончательной обработки и выбор средств измерения деталей
Способы окончательной обработки поверхностей деталей в соединении определяются по таблице 2.66 /3/.
Отверстие в корпусе - чистовое растачивание дает Rа = 1,6 - 3,2 мкм при достижимом квалитете точности JТ 7.
Наружная поверхность бронзовой втулки окончательно обрабатывается тонким (алмазным) точением при Rа = 0,4-0,8 мкм и экономическом квалитете точности JТ 7.
Контроль размеров деталей обеспечивается выбором инструмента, для которого предельная погрешность измерения (Dlim) не должна превышать допускаемую погрешность измерения (dизм ) по ГОСТ 8.051-81.
По таблице 7/4/ для измерения вала (посадочная наружная поверхность втулки) рекомендуются средства 4б, 5г, 6б, для которых допускаемая погрешность dизм = ±5 мкм. Выбираем из таблицы 1 /4/ гладкий микрометр, для которого предельная погрешность Dlim = ±5 мкм. При измерении микрометр устанавливается в стойку.
По таблице 7/4/ для измерения отверстия (внутренний диаметр чугунного корпуса) рекомендуются средства 6а, 9а, 12б, для которых допускаемая погрешность dизм = ±9 мкм.
Выбираем из таблицы 2 /4/ нутромер индикаторный с измерительной головкой с ценой деления 0,002 мм, для которого предельная погрешность Dlim = ±6,5 мкм.
2.9 Выполнение эскизов деталей соединения и узла в сборе
Для оформления рабочих чертежей и контроля деталей необходимы дополнительные данные. Эти данные относятся к конкретным деталям, поэтому в качестве примера рассмотрим посадку стакана в чугунный корпус редуктора (рисунок 1).
Для определения допусков формы принимаем относительную геометрическую точность формы нормальную (А) таблица 2.19/3/ со средним соотношением допусков формы и размера
Степени точности по таблице 2.20/3/ принимаются: для стакана (JT5) - пятая, корпуса (JT6) - шестая.
Числовые значения допусков цилиндричности по таблице 2.19/3/: для отверстия корпуса - 10 мкм, для стакана - 6 мкм.
Шероховатость поверхностей в соединении определяется в зависимости от квалитета и допуска формы по таблице 2.67 /3/.
Для отверстия Rа = 1,6 мкм, для стакана Rа = 0,8 мкм.
Вычертим эскизы деталей соединения с обозначением всех размеров.
![]() |
![]() |
|

![]() |
Узел в сборе Корпус Стакан
Рисунок 2.3 Эскиз посадки стакана в корпус.
Особенности анализа посадки с зазором
При анализе посадки с зазором определяются предельные и вероятностные зазоры, а в характеристике посадки и сводных данных приводятся полученные зазоры ( ).
3 ПОСАДКИ ПОДШИПНИКОВ КАЧЕНИЯ
При выборе посадок подшипников следует учитывать класс точности подшипника, вид нагружения колец подшипника и интенсивность нагружения узла подшипника (режим работы).
Диаметр вала - d= 40 мм;
Подшипник - шариковый однорядный;
Эквивалентная нагрузка - Р = 3.5 кН;
Режим работы - нормальный.
3.1 Обоснование характера работы подшипника
Заданный узел относится к редукторам общего машиностроения, которым не предъявляются особые требования к точности узла, ограничению вибраций, поэтому может быть принят класс точности подшипника «0» по ГОСТ 520 - 89.
Из чертежа узла видно, что вращается вал вместе с внутренним кольцом подшипника, а наружное кольцо установлено неподвижно в корпусе. На подшипник через вал передается нагрузка от зубчатой передачи постоянная по направлению. Отсюда следует, что на внутреннее кольцо действует циркуляционное, а наружное местное нагружение.
3.2 Расчет и выбор стандартного подшипника
Режим работы подшипника оценивается по интенсивности нагружения:
i=р/с, (15)
где р - динамическая эквивалентная нагрузка, Н;
с - динамическая грузоподъемность, Н.
Нагрузка на подшипник задана, а грузоподъемность приводится в стандартах на каждый тип и размер подшипника.
Поскольку в задании номер подшипника (размеры) не заданы, а указан режим работы и нагрузка, то, определив необходимую грузоподъемность можно выбрать размеры (серию) подшипника по заданному диаметру вала.
Для нормального режима работы по таблице 9 ГОСТ 3325 - 85 необходимо: 0,07 р/с 0,15, откуда 8200/с 0,15, когда с 3500 Н.
По таблице 7 ГОСТ 8338 - 75 для подшипника с внутренним диаметром d = 40 этому условно отвечает подшипник серии № 108, для которого С=16800 Н, наружный диаметр Д = 68, ширина кольца подшипника В = 15, координата фаски r = 1,6 мм. (стр. 253 /6/)
3.3 Выбор посадок колец подшипника
По таблице 1 приложения ГОСТ 3325 - 85 для подшипника «0» класса точности рекомендуется посадка LO/h6
Условное обозначение посадки «внутреннее кольцо – вал»: ,
где LО - означает поле допуска внутреннего кольца подшипника нулевого класса точности.
Эта посадка подшипника на вал имеет широкое применение в сельскохозяйственных машинах, редукторах, коробках скоростей станков, коробках передач автомобилей, тракторов и других машинах.
Для наружного кольца при местном виде нагружения, рекомендуется посадка в корпус Н7/l0 (таблица 3/4/).
Условное обозначение посадки «наружное кольцо – корпус»: ,
где l0 - означает поле допуска наружного кольца подшипника нулевого класса точности.
Эта посадка рекомендуется для узлов общего машиностроения, редукторов, сельскохозяйственных машин.
До последнего времени широко использовалась методика выбора посадок подшипников без учета их грузоподъемности /7/, /8/. Сравним эти две методики на примере задания.
Для циркуляционно-нагруженного кольца определяется интенсивность нагружения по формуле 4.25 /8/:
(16)
где PR - интенсивность нагружения, кН/м;
R- радиальная нагрузка кН;
в - рабочая ширина подшипника, м
, мм;
kn - динамический коэффициент;
F - коэффициент ослабления посадочного места;
FA - коэффициент неравномерности нагрузки для двухрядного подшипника.
По условию задания: kn =1, F = 1, FA = 1, R = 3,5 кН/м
PR = 3,5·1·1·1/(12)·10-3 = 291,6 кН/м
По таблице 4.92 /8/ рекомендуется поле допуска вала – h6.
По таблице 4.89 /8/ рекомендуется поле допуска корпуса - Н7.
3.4 Расчет посадки подшипника
Для расчета посадок колец подшипника на вал и в корпус отверстия; принимаются средние диаметры колец () и их допустимые отклонения (
) для полей допусков колец L0 и l0.
Для выбранных посадок отклонения посадочных мест вала и корпуса принимаются по ГОСТ 25347-86.
Предельные размеры вала и корпуса:
;
.
Предельные размеры внутреннего и наружного кольца подшипника:
,
;
,
.
Предельные зазоры и натяги в соединении «вал – внутреннее кольцо»: ;
«корпус – наружное кольцо»:
;
.
Допуск посадки в соединении:
«вал – внутреннее кольцо»:
.
«корпус – наружное кольцо»:
.
Проверка: ;
.
Схема полей допусков приведена на рисунке 3.1
![]() |
![]() |
![]() |
Рисунок 3.1 Схема полей допусков подшипника
Сводные данные по расчету посадок колец подшипника приведены в таблице 3.1.
Таблица 3.1 Расчётные характеристики посадок колец подшипника
Элементы соединения |
Наименование параметров |
Обозначение |
Величина |
||
Корпус-наружное кольцо подшипника |
Отверстие |
Отклонения, мкм |
Верхнее Нижнее |
|
+30 0 |
Предельные диаметры, мм |
Наибольший Наименьший |
|
68,030 68 |
||
Вал |
Отклонения среднего диаметра, мм |
Верхнее Нижнее |
|
0 -15 |
|
Предельные размеры среднего диаметра, мм |
Наибольший Наименьший |
|
40 39,988 |
||
Посадка |
Зазоры, мкм |
Наибольший Наименьший |
|
40 0 |
|
Внутреннее кольцо подшипника - вал |
Отверстие |
Отклонения среднего диаметра, мм |
Верхнее Нижнее |
|
0 -12 |
Предельные размеры среднего диаметра, мм |
Наибольший Наименьший |
|
68 67,985 |
||
Вал |
Отклонения, мкм |
Верхнее Нижнее |
|
+16 0 |
|
Предельные диаметры, мм |
Наибольший Наименьший |
|
40,016 40 |
||
Посадка |
Натяги, мкм |
Наибольший Наименьший |
|
28 0 |
4 ВЫБОР ПОСАДКИ ПО АНАЛОГИИ
Выбор по аналогии с существующими конструкциями машин и механизмов очень широко применяется на практике независимо от системы допусков аналога. При выборе по аналогии пользуется справочниками, описаниями конкретных машин, техническими условиями на капитальный ремонт и другими источниками.
Перед решением задачи необходимо проанализировать условия работы данного соединения. Если эти условия не вытекают из конструкции, то характер, нагрузок можно определить по другим соединениям, для которых условия работы заданы. Например, если для подшипников задан тяжёлый режим работы, удары, вибрация, нагрузки и т.п., то эти условия можно отнести и к другим деталям (шестерням, муфтам, шкивам и др.).
При выборе посадок следует учитывать условия сборки и разборки узла, возможность применении универсального инструмента, потребность в специальных приспособлениях. Особенно тщательно следует анализировать условия сборки для соединений с натягом, для которых монтаж и особенно разборка специфичны. Задавая ту или иную посадку, учитывать точность обработки соединяемых деталей. Стремиться к применению посадок возможно более низкой точности, при заданных нагрузках, которые проще выполнить на универсальных станках.
Для некоторых групп деталей установлены особые требования к посадкам, от которых зависит работоспособность узла и всей машины. К таким деталям относятся шестерни, шпиндели и направляющие станков, цилиндры и поршни различных машин, золотниковые пары и другие соединения.
Например, для установки шестерен должно быть обеспечено хорошее центрирование, учитывающее степень точности изготовления зубьев колеса, условия работы зубчатой пары в различных механиках. Эти требования приведены в таблице 5.25 /8/, которая рекомендует посадки для различных условий работы. Большой справочный материал по различным типам посадок приведен в литературе /3/.
1. Для узла, изображённого на рисунке 1 выбрать посадку распорной втулки по диаметру .
Эта шейка вала изготовлена под размер для посадки внутреннего кольца подшипника. Для посадки распорной втулки нужно выбрать поле допуска, обеспечивающее гарантированный зазор.
По ГОСТ 25346-89 выбираем основное отклонение отверстия +64 мкм, что соответствует обозначению поля допуска «F». При выборе данного поля допуска получается минимальный гарантированный зазор, обеспечивающий простоту разборки и сборки сопряжения. Квалитет для втулки выбираем из условия простоты обработки при изготовлении. Принимаем 8 квалитет, что может быть достигнут чистовым точением втулки /3/. Таким образом, получаем комбинированную (специальную) посадку:
Для выбранной посадки приведем схему полей допусков с указанием предельных размеров, отклонений, значений зазоров или натягов и эскиз соединения с указанием принятой посадки.
|
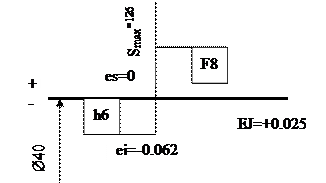
Рисунок 4.1 Схема полей допусков посадки для распорной втулки
2. Для узла, изображённого на рисунке 1 выбрать посадку распорной втулки по диаметру .
Эта шейка вала изготовлена под размер для посадки внутреннего кольца подшипника. Для посадки кольца нужно выбрать поле допуска, обеспечивающее гарантированный зазор. Кольцо служит для ограничения хода подшипника. Ударные нагрузки не испытывает. Центрирование не требуется.
Выбираем посадку
Рисунок 4.2 Схема полей допусков посадки для
3. Для узла, изображённого на рисунке 1 выбрать посадку крышки по диаметру .
Эта шейка вала изготовлена под размер для установки крышки. Крышка ограничивает и регулирует ход подшипника. Ударные нагрузки не испытывает.
Выбираем посадку
Рисунок 4.3 Схема полей допусков посадки для
5 ПОСАДКИ ШПОНОЧНОГО СОЕДИНЕНИЯ
При выборе посадок шпоночных соединений с сегментными шпонками следует руководствоваться требованиями ГОСТ 23360-78 стр.235-238 /8/, для сегментной шпонки следует руководствоваться ГОСТ 24071-81 таблицы 4.67-4.68.2 /9/, в которых даны размеры шпонок в зависимости от диаметра вала, размеры пазов, рекомендуемые длины шпонок, допуски, посадки, шероховатости для элементов шпоночного соединения.
5.1 Определение размеров шпоночного соединения
Размеры шпонки, предельные отклонения выбираются по таблице 4.64 /8/
Для диаметра вала d3
=43 сечение шпонки ,
размер фаски S от 0,4 до 0,6.
Длина шпонки, определяется по чертежу.
Ширина шпонки 10 мм;
Высота шпонки 13 мм;
Диаметр шпонки 22 мм.
5.2 Выбор полей допусков сопрягаемых размеров
Необходимые зазоры и натяги в шпоночном соединении получаются за счет допусков пазов, т.е. принимается система вала.
Предельные отклонения находим аналогично заданию 1: ширина 10h9 (-0,043 ), высота 13h9 (-0,11 ), на длину h14 . Длина шпонки 32h14(-0,62 ).
Допуски по ширине шпонки определяется ее назначением. В заданном узле по валу со шпонкой перемещается муфта. Поэтому принимается (таблица 4.65) свободное соединение, для которого ширина паза вала , ширина паза втулки
, длина паза вала
. Глубина паза вала
, паза втулки
, таблица 4.66 /9/, радиусы закругления пазов не менее 0,25 не более 0,4. Отклонения на размеры принимаются по ГОСТ 25347 -89 причем отклонения паза
следует брать из приложения 3- дополнительные поля допусков.
Рисунок 5.1 Схема полей допуска паза вала
Рисунок 5.2 Схема полей допуска паза втулки
5.3 Эскизы шпоночного соединения и сопрягаемых деталей
Данные для оформления рабочих чертежей деталей узла подшипника выбираются по ГОСТ 3325-85 /5/.
Шероховатость , не более: вала 1,25 мкм, отверстия 2,5 мкм, опорных торцов вала и корпуса 2,5 мкм.
Допуски формы посадочных поверхностей: для вала: допуск круглости 4 мкм и профиля продольного сечения 4 мкм; для корпуса: допуск круглости 9 мкм и профили продольного сечения 9 мкм.
Допуски торцового биения: заплечиков вала не более 25 мкм; заплечиков корпуса не более 54 мкм. Размеры заплечиков, берутся по ГОСТ 20226-82 /5/.
Эскизы деталей узла подшипника приведем на рисунке 5.1.
![]() |
![]() |
Рисунок 5.3 Эскизы деталей сопрягаемых с подшипником
Средства контроля размеров шпоночных соединений
Для дифференцированного контроля размеров деталей шпоночного соединения можно использовать универсальные средства измерения, однако это требует больших, затрат времени. Поэтому на предприятиях автотракторного и сельскохозяйственного машиностроения детали, шпоночных соединений контролируют с помощью предельных калибров. Ширину пазов валов проверяют пластинами, имеющими проходную и непроходную стороны. Размер от образующей цилиндрической поверхности втулки до дна паза контролируют пробкой со ступенчатым выступом. Глубину паза вала проверяют кольцевыми калибрами. При ремонте машин можно использовать как универсальные средства измерения, так и калибры.
Рисунок 5.1 Эскизы шпоночного соединения
6 РАСЧЕТ РАЗМЕРНОЙ ЦЕПИ
В курсовой работе решается прямая задача, в которой задан номинальный размер и допуск замыкающего звена; требуется определить допуски составляющих звеньев.
Задача решается расчетом на максимум - минимум, когда учитываются предельные отклонения звеньев и самые неблагоприятные их сочетания, а также вероятностным расчетом с учетом рассеяния размеров и вероятности различных сочетаний отклонений составляющих звеньев размерной цепи.
В основу решения положен метод равноточных допусков, когда определяется квалитет для всех звеньев размерной цепи, находятся допуски и отклонения каждого звена.
Задано замыкающее звено:
6.1 Составление размерной цепи
При составлении размерной цепи необходимо уяснить, что представляет замыкающее звено, как оно образуется и на что влияет. Выявить детали, влияющие на размер замыкающего звена, рисунок 7.1.
В заданном примере замыкающее звено это зазор между крышкой подшипника 4 и корпусом 9. Зазор образуется при затяжке винтов крепления крышки к корпусу, когда стягивается пакет деталей, включающих: ширину кольца
, ширину
наружного кольца шарикоподшипника 5, ширину второго подшипника
,и толшинц буртика вала
.
Замыкающее звено необходимо для осевой фиксации наружного кольца подшипника и лабиринтного кольца.
![]() |
![]() |
![]() |
|
![]() |
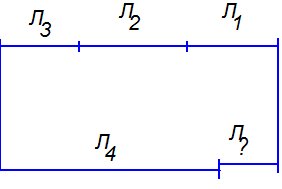
![]() |
![]() |
![]() |
Рисунок 7.1 Схема размерной цепи
Общее количество звеньев- 4;
Звенья Л1
,Л2
,Л3
- увеличивающее ()
Звено Л4
- уменьшающее ().
6.2 Определение размеров звеньев
Размеры подшипника и его допуски известны из задачи 4. Ширина наружного кольца мм, т.е.
мм.
Полученные длины звеньев округляются до нормальных линейных размеров по ГОСТ 6636 - 69 таблице 1.3 /3/
Для согласования длин звеньев в размерной цепи используется основное уравнение (80) /7/
(17)
где - число увеличивающих звеньев;
- число уменьшающих звеньев.
, (18)
подставляя значения, получим:
2 мм=(18+18+4)-43=-3 мм;
Корректируем мм.
6.3 Расчет размерной цепи на максимум, минимум. Определение среднего коэффициента точности (95) /7/:
; (19)
где - средний коэффициент точности;
- допуск замыкающего звена;
мкм
- число звеньев с известными допусками;
- допуски известных звеньев (
);
- число звеньев размерной цепи, для которых определяется средний коэффициент точности;
- единица допуска размера звена, выбирается по таблице 7.1.
Таблица 7.1 Значение единиц допусков
Размер, мм |
0 |
3 |
6 |
10 |
18 |
30 |
50 |
80 |
120 |
180 |
250 |
315 |
400 |
3 |
6 |
10 |
18 |
30 |
50 |
80 |
120 |
180 |
250 |
315 |
400 |
500 |
|
i, мкм |
0,55 |
0,73 |
0,90 |
1,08 |
1,31 |
1,56 |
1,86 |
2,17 |
2,52 |
2,89 |
3,22 |
3,54 |
3,89 |
Тогда:
По ГОСТ 25346-89 таблица 5 ближайшее значение коэффициента точности аср =64, соответствующее 10 квалитету.
Назначение отклонений звеньев:
На звено отклонения заданы
. Звено
имеет охватываемую поверхность и на него назначаются отклонения, как на основной вал:
Звено на него отклонения вычисляются как на корректирующее звено из уравнений для корректирующего звена (94) /7/:
Результаты расчёта размерной цепи на максимум-минимум:
Проверка ,
что соответствует принятому допуску звена.
Проверка принятых допусков и их корректировка:
; (20)
;
Проверка:
6.4 Расчет размерной цепи вероятностным методом
Коэффициент точности размерной цепи (102) /7/:
(21)
По ГОСТ 25346 - 89 таблица 5, ближайшее значение коэффициента точности , соответствующее 13 квалитету:
Проверка и корректировка допусков:
Необходима корректировка допусков в сторону уменьшения допусков для звена как наиболее простого в изготовлении, принимаем допуск по 12 квалитету:
Корректировка проведена правильно. 400305,9
Назначение отклонений на размеры:
Аналогично принимаются отклонения для всех звеньев, кроме корректирующего звена
Определение отклонений корректирующего звена:
Для определения отклонений корректирующего звена используется уравнение (87) /7/:
где
-среднее отклонение замыкающего звена;
- средние отклонения увеличивающих звеньев;
- средние отклонения уменьшающих звеньев
Отклонения корректирующего звена:
Результаты расчета размерной цепи вероятностным методом:
Сравнение результатов расчетов размерной цепи на максимум-минимум и вероятностного:
Применение вероятностного метода расчета позволяет увеличить допуски, звеньев в 2 - 2,5 раза.
Результаты расчета размерной цепи сведены в таблицу 7.2
Таблица 7.2 Результаты расчёта размерной цепи
Параметры размерной цепи |
Звенья размерной цепи |
||||||
Обозначение звена |
ЛD |
Л1 |
Л2 |
Л3 |
Л4 |
||
Вид звена |
замык |
увелич |
увелич |
увелич |
уменьш |
||
Размер, |
|
4 |
18 |
18 |
38 |
||
Единица допуска, мм |
- |
0,73 |
- |
1,56 |
|||
Расчёт на максимум-минимум |
|||||||
Значение допусков, мкм |
табличн. |
- |
75 |
- |
- |
100 |
|
принятые |
400 |
48 |
120 |
120 |
112 |
||
Отклонение, мкм |
верхнее |
0 |
0 |
0 |
0 |
+112 |
|
нижнее |
-400 |
-48 |
-120 |
-120 |
0 |
||
Размеры звеньев с отклонениями |
|
|
|
|
|
||
Вероятностный расчет |
|||||||
Значение допусков, мкм |
табличн. |
- |
75 |
- |
- |
390 |
|
принятые |
400 |
48 |
120 |
120 |
250 |
||
Отклонение, мкм |
верхнее |
0 |
0 |
0 |
0 |
251 |
|
нижнее |
-400 |
-48 |
-120 |
-120 |
-69 |
||
Координата середины поля допуска, мкм |
-200 |
0 |
-60 |
-60 |
125 |
||
Размеры звеньев с отклонениями |
|
|
|
|
|
ЗАКЛЮЧЕНИЕ
В заключении необходимо отметить, что вероятностный метод позволяет получить более грубые и более дешевые квалитеты при малой вероятности брака по сравнению с методом полной взаимозаменяемости.
Плюсы очевидны, поэтому предпочтительнее делать все расчеты вероятностным методом как более эффективным и экономически выгодным.
БИБЛИОГРАФИЧЕСКИЙ СПИСОК
1 Кудряшов Д.Н., Попов В.И. Взаимозаменяемость, стандартизация и технические измерения. Альбом чертежей.-М,:1993.-43 с.
2 Рекомендации по внедрению СТ СЭВ 144-75 и СТСЭВ 146-75 на допуски и посадки гладких соединений с размерами до 3150 мм. Издательство стандартов.-М.:1977.-52 с.
3 Мягков В.Д. Допуски и посадки. Справочник. Ч.1 -Д.: Машиностроение, 1982. -541 с.
4 Методические указания. Выбор универсальных средств измерений линейных, размеров до 500 (по применению ГОСТ 8.051-81) РД50-98-86.-М.:Издательство стандартов, 1987. -83 с.
5 Подшипники качения. Сборник государственных стандартов. Ч.1 -М.: Издательство стандартов, 1989, -439 с.
6 Подшипники качения. Сборник государственных стандартов. Ч.2 -М.: Издательство стандартов, 1989, -432 с.
7 Серый И.С, Взаимозаменяемость, стандартизация и технические измерения. -М.: Агропромиздат, 1987, - 360 с.
8 Мягков В.Д. Допуски и посадки. Справочник. Ч.2 -л.: Машиностроение, 1983. -446 0.