Разработка технологического процесса сборки и монтажа блока РЭА
СОДЕРЖАНИЕ: СОДЕРЖАНИЕ 4.1 Анализ вариантов маршрутной технологии 40 4.2 Выбор оптимального варианта по производительности 44 4.3 Выбор технологического оборудования 48СОДЕРЖАНИЕ
1. Анализ процессов и устройств для сборки и монтажа
2. Анализ технологичности конструкции изделия
3. Разработка технологической схемы сборки
4.1 Анализ вариантов маршрутной технологии
4.2 Выбор оптимального варианта по производительности
4.3 Выбор технологического оборудования
4.4 Разработка маршрутно-операционной технологии
5. Проектирование участка сборки и монтажа
6. Разработка оснастки для сборочно-монтажных работ
7. Требования по технике безопасности и охране труда
Список использованных литературных источников
Приложение А Сборочный чертеж
Приложение Б Технологическая документация
Приложение В План участка цеха
Приложение Г Чертеж оснастки
ВВЕДЕНИЕ
Целью данного проекта является разработка технологического процесса сборки и монтажа печатного узла двухканальной системы сбора и обработки данных (ССОД) на базе персонального компьютера.
Одно из основных требований к прибору – доступная цена и необходимая функциональность, что делает его конкурентоспособным по сравнению с аналогичными устройствами. Для достижения данного эффекта следует разработать такой технологический процесс, который являлся бы наиболее эффективным.
Необходимость в разработке данного устройства обусловлена его универсальностью для контроля технологических процессов производимых на производствах различного профиля, так как входной величиной является аналоговый сигнал (напряжение), а выходным – данные измерений. При небольшой доработке программного обеспечения можно получить систему сбора, обработки данных и управления установками техроцесса на основании полученных данных.
В процессе выполнения проекта решаются следующие задачи:
1. Анализ процессов и устройств для сборки и монтажа;
2. Анализ технологичности конструкции изделия;
3. Разработка технологической схемы сборки;
4. Анализ вариантов маршрутной технологии;
5. Выбор технологического оборудования;
6. Проектирование технологического процесса;
7. Проектирование участка сборки и монтажа;
8. Разработка оснастки для сборочно-монтажных работ;
9. Требования по технике безопасности и охране труда;
10. Разработка комплекта технологической документации.
Изделие представляет практический интерес, т.к. выполнено на современной, надежной и многофункциональной элементной базе. Благодаря этому устройство отличается схемотехнической простотой с одновременной многофункциональностью и гибкостью. Это способствует увеличению надежности работы устройства, упрощению его ремонта.
Конечным результатом выполнения проекта будет комплект технологических документов.
1. АНАЛИЗ ПРОЦЕССОВ И УСТРОЙСТВ ДЛЯ СБОРКИ И МОНТАЖА
Технологические процессы могут осуществляться либо вручную, либо с применением оборудования. Оборудование подразделяется на универсальное и специализированное. На универсальном оборудовании могут выполняться несколько различных операций. Специализированное оборудование используется для выполнения одной конкретной операции. Универсальное оборудование используют при крупносерийном и массовом производстве. Специализированное - целесообразно применять при серийном и единичном производстве.
Операции, используемые при различных типах сборки:
- нанесение пасты и установка SMD компонентов на верхнюю сторону платы;
- нанесение пасты и установка SMD компонентов на нижнюю сторону платы;
- нанесение клея и установка SMD компонентов на нижнюю сторону платы с последующим его высыханием;
- автоматическая установка DIP компонентов;
- автоматическая установка координатных компонентов (такие как светодиоды и т.п.);
- ручная установка других компонентов;
- пайка волной или пайка инфракрасным излучением;
- промывка плат;
- ручная пайка компонентов.
Рассмотрим подробнее процессы и устройства, которые могут применяться для сборки и монтажа современных радиоэлектронных блоков. Для сборки печатного узла (установки на поверхность печатной платы ИЭТ) может использоваться как автоматизированное оборудование, так и ручная установка. Последнее оправдано в единичном и мелкосерийном производстве. При автоматизированной установке существует возможность выбора между автоматическими линиями установки ИЭТ по программе ЭВМ и сборкой при помощи пантографов или светомонтажных столов. В нашем случае оптимальным вариантом сборки ИЭТ на печатной плате будет их установка с использованием автоматизированного оборудования. Установка, крепление на плате и монтаж ИЭТ в сложных корпусах будет производиться вручную.
Так как в разрабатываемом устройстве применен смешанный вариант установки поверхностно-монтируемых и традиционных (монтируемых в отверстия) компонентов на одной стороне печатной платы, то для уменьшения общего числа операций монтажа и термического воздействия на компоненты целесообразным будет производить пайку поверхностно-монтируемых компонентов оплавлением в печи, а расположенных на этой же стороне печатной платы традиционных компонентов - волной припоя. Монтаж планарных элементов на печатной плате расплавлением дозированного количества припоя с использованием ИК-нагрева (оплавлением в печи) позволяет проводить соединения как индивидуальным, так и групповым способом, его целесообразно применять в серийном и массовом типе производства. Достоинства метода в следующем: оптимальные и управляемые скорости нагрева; возможность пайки только с одной стороны платы; низкая стоимость процесса. Пайка компонентов, монтируемых в отверстия, волной припоя характеризуется теми же достоинствами, что и пайка оплавлением в печи.
Фиксация ИЭТ, установленных на печатную плату до пайки может осуществляться приклейкой или подгибкой выводов. В данном случае оптимальным вариантом будет фиксация ИЭТ, монтируемых в отверстия, подгибкой выводов, а поверхностно-монтируемых элементов – при помощи паяльной пасты, наносимой на контактные площадки и обладающей достаточной адгезионной способностью. Кроме того, такой способ установки поверхностно-монтируемых элементов хорош тем, что при пайке оплавлением происходит самоориентирование компонентов на контактных площадках, обусловленное действием сил поверхностного натяжения [ ].
Для нанесения паяльной пасты применим метод трафаретной печати, позволяющий наносить паяльную пасту на контактные площадки через металлические и сетчатые шаблоны в ручном, полуавтоматическом или автоматическом режиме с высокой точностью дозировки. Достоинство данного метода в его относительной простоте, а относительно высокая стоимость металлического трафарета для нанесения паяльной пасты оправдывается при серийном производстве.
Герметизация смонтированного печатного узла – покровная – т.е. производится покрытие ИЭТ (за исключением элементов поз. ) и печатной платы лаком ЭФ-9-080 ТУ 2389-030-00216415-2001. Покрытие осуществляется вручную кистью.
Для снижения количества брака при проведении сборочно-монтажных работ необходимо предусмотреть после проведения наиболее сложных и ответственных операций (автоматизированная установка и пайка ИЭТ) проведение контрольных операций. Контроль может быть как автоматизированным (системы технического зрения), так и визуальным. В данном случае ввиду невысокой плотности монтажа и использования интегральных микросхем с небольшим числом выводов достаточным будет использование визуального контроля.
Внедрение новых систем автоматизации и оборудования позволяет сократить время технологического цикла на величину до 50%. Новые средства автоматизации позволяют также лучше предсказывать уровень выхода годных изделий и оптимизировать его.
Оборудование, используемое для производства ИЭТ.
1.1 Нанесение паяльной пасты, клея
- Дозатор MD40 фирмы Mechatronika.
Дозатор MD40 - это профессиональное оборудование для нанесения паяльной пасты и клея. Данный автомат идеален для производственных участков с небольшой площадью. Можно порекомендовать данную систему для мелкосерийных производств. Оборудование имеет хорошую точность позиционирования по осям X и Y и достаточно высокую скорость (до 15 000 доз в час). Бесперебойную работу и простоту технического обслуживания обеспечивает продуманная архитектура автомата.
Рисунок 1.1 - Установка дозирования для нанесения паяльной пасты MD40
-
Дозаторы Camalot XyfexPro+, XyfexPro+SMT фирмы Speedline.
Дозаторы Camalot XyfexPro+ и XyfexPro+SMT обладают:
а). высокой скоростью и точностью дозирования;
б). дозирующей головкой с линейными сервоприводами;
в). XyfexPro+SMT- только для поверхностного монтажа;
г). одинарной или двойной конфигурацией головы дозатора;
д). запатентованной системой взвешивания дозы, обеспечивающей автоматический контроль объема дозы для избежания снижения качества из-за изменений в составе материала;
е). автоматической системой очистки иглы;
ж). всеми видами дозирования: точка, линия, заливка и т.д.
Рисунок 1.2 - Установка дозирования для нанесения паяльной пасты Camalot Xyfex
-
Установка трафаретной печати Ekra Е1.
Полуавтоматический принтер E1 - система, идеально подходящая для использования на производстве с небольшими объемами выпускаемой продукции, но с частыми изменениями ассортимента. В концепцию принтера включено продуманное сочетание цена/качество/скорость. При применении на производстве принтера E1, пользователь получает возможность максимально сокращать потери непроизводственного времени за счет возможности быстрой перенастройки принтера на выпуск нового изделия. Продуманная конструкция печатающего устройства и рабочего стола принтера гарантирует точность нанесения вещества через трафарет на поверхность печатной платы и хорошую повторяемость в течение рабочего цикла. Принтер оборудован компьютером, в память которого могут быть внесены 99 программ печати как односторонних, так и двусторонних печатных плат. Опционально принтер оборудуется полуавтоматической видеосистемой, которая позволяет значительно увеличить производительность производства.
Рисунок 1.3 - Полуавтоматический принтер трафаретной печати Ekra Е1
- Установка трафаретной печати Exerra eP20.
Установка обладает следующими свойствами:
- устойчивая монолитная станина с гранитным рабочим столом;
- управление силой давления ракелей с обратной связью;
- управление работой всех осей сервомоторами с оптической связью;
- высокоточное совмещение трафарета и платы;
- дружественный пользовательский интерфейс;
- мощная система 2D-контроля качества нанесения паяльной пасты и засорения апертур трафарета.
1.2Установка компонентов
- Полуавтомат для установки SMD-компонентов MM500.
Полуавтоматический манипулятор MM500 фирмы Mechatronika предназначен для установки SMD-компонентов. Используется для сборки мелких и опытных серий несложных изделий.
Достоинства:
а). простота работы и программирования, надежность, низкая стоимость;
б). встроенный пневматический программируемый дозатор паяльной пасты или клея;
в). встроенный компьютер (не требует дополнительного компьютера и места под него);
г). автоматическая карусель с 45/90 ячейками для компонентов из россыпи;
д). ПО для программирования на отдельном компьютере. Позволяет импортировать из CAD-приложений координаты и хранить архивы программ;
е). видеокамера и монитор для обзора печатной платы на мониторе;
ж). ручные и автоматические питатели для лент и пеналов.
Рисунок 1.4 - Полуавтомат для установки компонентов MM500
- Автоматы для установки компонентов поверхностного монтажа серии MY.
Автоматы MYDATA (Швеция) являются одними из признанных лидеров в точности и скорости перехода с одного изделия на другое. Скорость заправки современных питателей от MYDATA исчисляется секундами. Сокращение времени простоя приводит к тому, что при равных скоростных характеристиках, указанных по IPC 9850, в конце рабочей смены линия с автоматом MYDATA выпускает на 20-50% большее количество продукции. Высокая точность позволяет автоматам MYDATA осуществлять сборку, соответствующую самым жестким современным требованиям. Число в названиях моделей обозначает количество мест под питатели и сборочный стол (например, MY9 – 9 мест, из которых рабочий стол занимает минимум 3 места и т.д.). Установщик типа MY9 обеспечивает общую емкость питателей в 96 восьмимиллиметровых лент с компонентами, а установщики MY12, MY15 и MY19 обеспечивают общие емкости в 144, 192 и 256 лент соответственно (при установке сборочных столов, занимающих 3 места). При этом при заказе машин с большими сборочными столами максимальное количество питателей может уменьшиться. Во всех установщиках, производимых MYDATA, питатели установлены со стороны оператора машины. Также в обозначении могут присутствовать буквы Е и ECR (например, MY9E или MY9ECR). Машины с индексом Е (Extended) в базовой версии имеют высокоскоростной модуль с линейной камерой и конвейерный стол с линейным приводом. Машины с индексом ЕCR (Extended component range) – это машины, специально рассчитанные на установку компонентов нестандартных размеров. Например, устанавливаемый компонент может быть 132 мм, высотой 40 мм и весом до 300 грамм! Еще одна особенность машин – раздельное перемещение по осям, что в сочетании с высокопрочной цельной станиной обеспечивает очень стабильное и точное позиционирование монтажного модуля. Благодаря тому, что все питатели электронные и с линейным приводом, воздух необходим только для захвата и монтажа компонентов. Его потребность обеспечивает встроенная в машину помпа.
Рисунок 1.5 - Автомат для установки компонентов серии MY
Для установки элементов, монтируемых в отверстия, возможно использование следующего оборудования:
- монтажная станция Royonic 550 (Royonic, Германия) (рисунок 1.6).
Рисунок 1.6 – Монтажная станция Royonic 550
Особенности:
- эргономичный дизайн;
- удобство эксплуатации;
- возможность объединения установок в сеть.
Таблица 1.1 – Технические характеристики Royonic 550
Наименование: | Параметр: | Примечание: |
Количество магазинов: | 78 шт. | Размер магазина: 620 х 105 х 50 мм |
Количество ячеек: | 624 шт. | Размер одиночной ячейки: 73 х 88 x 45 мм .Также возможно разделение ячеек при помощи перегородок. Другие размеры ячеек также возможны. |
Скорость установки компонентов: | до 1600 комп./час. | Типовой диапазон составляет 700 – 1000 комп./час |
Скорость подачи ячейки: | 3 сек. | скорость подачи приблизительно 30 ячеек/сек. |
Ошибка: | 0,02% | - |
Защита компонентов: | имеется | Магазины и ячейки выполнены из токопроводящего пластика, а также заземлены. Проводимость поверхности стола и проводов заземления выполнены согласно ISO 9000 и Европейских норм. |
Напряжение питания: | 100 – 230 В/ 50-60 Гц, 650 Вт | - |
Источник светового луча: | галогенная лампа 6В / 10 Вт | опционально поставляется лазерный источник |
Занимаемая площадь: | 1000 x 1560 мм | - |
Вес: | 350 кг. | - |
1.3 Оплавление
После нанесения паяльной пасты и установки элементов следует этап оплавления. Для этого используют печи, которые отличаются количеством зон нагрева и методом подогрева — инфракрасным, конвекционным, смешанным.
Инфракрасные печи имеют низкую цену и применяются при изготовлении несложных плат. Обусловлено это тем, что инфракрасный тип нагрева имеет целый ряд отрицательных эффектов. Наиболее существенно влияют на работу следующие:
- теневой эффект. Высокие элементы могут закрывать более низкие, создавая так называемую тень, то есть зону, где высока вероятность непропая. Также некоторые элементы могут закрывать свои собственные выводы;
- существенное влияние на процесс пайки оказывает отражающая способность корпуса элемента;
- нестабильность распределения температуры внутри отдельных зон.
Всех этих отрицательных моментов лишены печи с конвекционным методом нагрева. Горячий воздух распределяется внутри рабочего объема печи таким образом, что в каждой точке создаются одинаковые условия пайки, одинаковая температура. Зависимость от отражающих качеств элемента отсутствует.
Но управлять горячим воздухом труднее и выполнять это технически также сложнее. Поэтому конвекционные печи имеют цену значительно выше.
- Печи оплавления припоя Heller серии Mark III.
Печи оплавления припоя Heller серии Mark III выпускаются с семью, девятью и тринадцатью зонами оплавления.
Особенности печи:
а). работа по свинцовой и бессвинцовой технологии;
б). компактный дизайн;
в). энергосберегающий дизайн, позволяющий минимизировать потребление электроэнергии;
г). экономный расход азота;
д). большее количество зон нагрева по сравнению с печами других производителей позволяет создать максимально плавный рост температурного профиля;
е). нижний подогрев в стандартной комплектации;
ж). система удаления флюса (Gen 5.2 и Gen 9.2) с функцией самоочистки без приостановки производства;
з). возможность считывания штрих-кодов для отслеживания продукции;
и). ECD – встраиваемое программное обеспечение для отслеживания условий производства и получаемого качества продукции;
к). автоматическая смазка конвейера;
л). соответствие международным стандартам.
На рисунке 1.7 представлен внешний вид печи Heller серии Mark III.
Рисунок 1.7 - Печь оплавления припоя Heller серии Mark III
В таблице 1.2 представлены технические характеристики печи оплавления припоя Heller серии Mark III.
Таблица 1.2 - технические характеристики печи оплавления припоя Heller серии Mark III
1707МК III | 1809MKIII | 1913MKIII | |
Габаритные размеры (ШхГхВ) | 3400х1370х1600 мм | 4650х1370х1600 мм | 5890х1370х1600 мм |
Количество зон нагрева | 7 (1830 мм) | 9 (2650 мм) | 13 (3650 мм) |
Количество зон охлаждения | 1 (350 мм) | 3 (750 мм) | 4 (1000 мм) |
Макс. ширина платы | 460 мм (опционально 710 мм ) | ||
Макс. температура нагрева | 350° С | ||
Электропитание | 3 х 380 В / 50 Гц |
- Инфракрасная печь оплавления припоя MR10A фирмы MECHATRONIKA.
Предназначена для оплавления припоя или полимеризации клея. Печь снабжена микропроцессорным управлением и позволяет запоминать до 16 профилей нагрева. Время одного цикла работы 4 - 10 минут. Проста в обращении и не требует специального технического обслуживания.
Рисунок 1.8 - Инфракрасная печь оплавления припоя MR10A
Печь обладает следующими техническими характеристиками:
1.4 Подготовка выводов компонентов
Рисунок 1.9 – Высокопроизводительная автоматическая система обрезки и формовки выводов CompactLine
- Высокопроизводительная система Compact Line™ предназначена для автоматической обрезки и формовки выводов для всех существующих на сегодняшний день типов корпусов.
Одним из главных достоинств системы Compact Line™ является инструмент, изготовленный по уникальной технологии и способный выдерживать до 5 000 000 циклов.
Вместительные магазины для подачи и выпуска изделий, двухстековая загрузка и выгрузка магазинов позволяют достигнуть высочайших показателей произоводительности (до 250 циклов/мин).
- Новая пневматическая двухцилиндровая установка для обрезки и формовки радиальных компонентов из россыпи и ИМС модель TP/ ТS 1.
Рисунок 1.10 – Установка для обрезки и формовки радиальных компонентов модель TP/ ТS 1
Установка оснащена разнообразными формовочными матрицами для выполнения различных формовок радиальных радиоэлементов и микросхем, имеет усиленные детали, позволяющие формовать большие компоненты. Обеспечивается формовка компонентов с максимальной длиной 140 мм и максимальным шагом между выводами – 45 мм.
- Диаметр выводов: 0,3 – 1,2 мм.
- Производительность: 2000 компонентов/час.
- Габариты : 230 x 390 x 140 мм.
Рисунок 1.11 – Машина для формовки аксиальных (осевых) компонентов TP6/PR-F
Основные особенности:
- формовка и обрезка выводов диаметром, мм: от 1 до 1,4 осевых
компонентов
- производительность, шт./час: до 25.000
- габариты (Ш x Д x В), мм: 180 x 230 x 210
- вес, кг.: 6
Модель TP6/PR-F была разработана для формовки и обрезки выводов осевых компонентов. Существует 3 версии данной модели для выводов диаметром: от 0,5 до 0,9 мм; от 0,8 до 1 мм и от 1 до 1,3 мм. Существует несколько формовочных матриц (шаблонов) на выбор для каждой из трёх версий. Формовочные матрицы заказываются отдельно согласно требуемой формы изгиба и диаметра выводов компонента. Качество и надёжность этих машин гарантируют высокую производительность.
Машина может быть оснащена питателем CS40 для подачи компонентов из россыпи. Дополнительно машину можно оснастить автоматическим приводом с регулятором скорости MOT98/A, управляемым от педали. При работе с компонентами в ленте рекомендуется использовать штатив BR6. Mодуль TNS помогает удалять остатки ленты.
1.5 Пайка волной
- Система пайки волной припоя ELECTROVERT VectraElite.
Особенности системы:
- работа по свинцовой и бессвинцовой технологии;
- удобный и быстрый доступ к системе;
- возможные системы флюсователей: ServoSpray и Performa;
- насадки UltraFill™ для работы по бессвинцовой технологии;
- конвекционный и ИК-преднагрев;
-ширина платы - до 460 мм;
- длина зоны предварительного нагрева - до 1,8 м.
Рисунок 1.12 - Системапайкиволнойприпоя ELECTROVERT VectraElite
Технические характеристики:
Габаритные размеры (ДхШхВ) 3117(3925)*х1557х1727 мм
Макс. ширина платы 457 мм
Максимальное кол-во флюсователей 2
Автоматическая регулировка ширины конвейера Опционально
Преднагрев 1200 (1800)* мм
УстанавливаемыеволныcoN2tour, Lambda, Rotary
chip, ExactaWave, UltraFill
УстранениеперемычекAccuknife, conN2tour PLUS
1.6 Отмывка
После пайки с платы необходимо удалить остатки флюса, если не применяется паста с флюсом, не требующим отмывки. Отмываются платы любым традиционным способом с учетом того, какая жидкость требуется для качественной отмывки флюса, применяемого в пасте, с помощью которой была произведена пайка.
Рассмотрим некоторые виды установок для отмывки.
- Системыотмывки Electrovert Aquastorm 100, 200, 200TZ.
Системы отмывки Aquastorm компании Electrovert, входящей в состав корпорации SpeedlineTechnologies, предназначены для отмывки электронных модулей.
Благодаря запатентованной насадке Hurricane Jet™ отмывочная жидкость способна проникать под высоким давлением под компоненты с малым шагом. Высокоточные струи распылителей JIC смывают даже самые трудноудаляемые остатки загрязнений. Насадка VeeJet формирует рисунок перехлестывающихся струй по всей ширине конвейера. Воздушный нож Electrosonic™ формирует прямой поток воздуха под высоким давлением для достижения высокого качества сушки.
Electrovert Aquastorm 100.
Система предназначена для работы с водосмываемыми, органическими и кислыми флюсами.
Electrovert Aquastorm 200.
Двухэтапная система отмывки, пригодная для работы с флюсами RMA (для которых нужны омыляющие реагенты), водосмываемыми, органическими и кислыми флюсами. Повышенная надежность безотмывного процесса.
Electrovert Aquastorm 200 TZ (Torrid Zone).
Оснащена модулем сушки с принудительной конвекцией, идеально подходящим для сложных случаев сушки плат.
На рисунке 1.13 представлен внешний вид системы отмывки ElectrovertAquastorm 100, 200, 200TZ.
Рисунок 1.13 - система отмывки ElectrovertAquastorm 100, 200, 200TZ.
- Система отмывки Accel HydroCel.
Система отмывки HydroCel компании Accel входящей в состав корпорации Speedline Technologies предназначена для отмывки малогабаритных электронных модулей, таких как гибридные платы и многокристальные модули (МКМ), индикаторные панели и кремниевые подложки, корпусированные полупроводниковые устройства, например BGA, по отдельности или по несколько штук.
HydroCel - это компактная полуавтоматическая система отмывки, отличающаяся высоким качеством отмывки, сушки и переработки моющей жидкости.
Во время цикла отмывки изделие, вращаясь, погружается в растворитель. Центробежная сила и сила Кориолиса заставляют растворителю двигаться параллельно плоскости изделия и проникать под компоненты, установленные даже на очень малом расстоянии от платы, и в глухие отверстия. Затем при необходимости следует цикл ополаскивания деионизированной водой. Во время цикла струйного ополаскивания HydroCel еще раз подает растворитель сверху и снизу вращающегося изделия, чтобы смыть остатки загрязнений и смыть растворитель. Во время сушки изделие непрерывно вращается, при этом в камеру подается горячий воздух или азот.
HydroCel совместима с большинством отмывочных жидкостей, в т.ч.: деионизированной водой, растворами на водной основе, а также большинством промышленных растворов, используемых при производстве электронных печатных плат и гибридных систем.
На рисунке 1.14 представлен внешний вид системы отмывки Accel HydroCel.
Рисунок 1.14 - Система отмывки Accel HydroCel.
- Система отмывки MINICLEAN.
Применяется в мелкосерийном производстве для отмывки от остатков флюса трафаретов, печатных плат/узлов, а также механических деталей.
Существует две модификации модулей: А и В для различных видов отмывки. Каждая модификация имеет четыре вида мойки.
Виды процессов отмывки: ультразвуковая отмывка на основе растворителя или технологии MPC (модуль A); отмывка на основе технологии MPC распылением в воздухе (модуль B); ополаскивание проточной водой (модули A и B); ополаскивание деионизированной водой (модули A и B); сушка горячим воздухом (модули A и B).
Технические характеристики:
Габаритные размеры модуля А 160x400x350 / 240x400x350
/ 240x430x380 мм
Габаритные размеры модуля B 100x600x650 мм
Размеры установки
(модуль без / с устройством деионизации воды) 1000x790x1450/
1000x1010x1450 мм
Электропитание 3 x 400 В/380 В, 50 Гц, 8,5 кВт
Мощность ультразвука 500, 750, 1000 Вт (зависит
от размеров мойки)
Ультразвуковая частота 40 кГц
На рисунке 1.15 представлен внешний вид системы MINICLEAN.
Рисунок 1.15 - Система отмывки MINICLEAN.
- Ультразвуковые ванны BlO-Chem
Ультразвуковые системы BlO-Chem предназначены для очистки печатных плат, компонентов, металлических изделий от остатков всевозможных химических материалов применяемых в соответствии с технологией обработки. Устройства сделаны из устойчивого к коррозии материала и могут применяться для работы с любыми невзрывоопасными жидкостями.
УЗ-генератор может работать в трех режимах:
- амплитудное колебание мощности УЗ с частотой 0,5 с;
- УЗ-пульсация с частотой 0,5 с;
- постоянная частота без изменения интенсивности.
Все устройства имеют удобный слив жидкости через специальное технологическое отверстие. Пульт управления устройством очень прост в работе и не требует специальных навыков оператора.
Рисунок 1.16 - Ультразвуковая ванна BlO-Chem
Технические характеристики ультразвуковой ванны BlO-Chem приведены в таблице 1.3.
Таблица 1.3 - Технические характеристики ультразвуковой ванны BlO-Chem
Модель | Частота, кГц | Размеры ванны, мм | Объем ванны, л |
G13915 | 35 | 240x137x100 | 2,75 |
G13925 | 35 | 300x150x150 | 5,75 |
G13935 | 35 | 300x240x150 | 9,5 |
G13945 | 35 | 300x240x200 | 12,75 |
G13910 | 35 | 327x300x200 | 18 |
G13920 | 35 | 505x300x200 | 28 |
G13930 | 45 | 500x300x300 | 45 |
G13940 | 45 | 600x500x300 | 90 |
G13950 | 25/45 | 330x300x230 | 25 |
G13960 | 25/45 | 500x300x350 | 55 |
G13970 | 25/45 | 500x300x500 | 80 |
G13980 | 25/45 | 600x500x350 | 115 |
G13990 | 25/45 | 600x500x500 | 160 |
1.7 Герметизация
Способы влагозащиты:
- погружением;
- распылением.
Рассмотрим установку влагозащиты погружением DS101.
Рисунок 1.17– Установка влагозащиты погружением DS101
Таблица 1.4 – Технические характеристики установки влагозащиты погружением DS101
Габаритные размеры ванн (дл. х шир. х глуб.), мм | 295 х 125 х 400 345 х 125 х 400 395 х 125 х 400 |
Емкость ванн, л | 14, 16, 18 |
Глубина погружения max, мм | 300 |
Диапазон регулирования скоростей погружения/извлечения, мм/мин | 25 - 300 |
Допуск на толщину покрытия, % | 5 |
Пневмопитание (сж.воздух), кгс/см2 | 5.5 |
Расход сж.воздуха, м3/мин | 0.14 |
Габаритные размеры, мм | 800 х 450 х 1060 |
Вытяжная вентиляция, куб. м/час | 620 |
- Раздельная регулировка скорости погружения и извлечения ПУ.
- Система контроля вязкости покрытий.
Конструктивно установка влагозащиты выполнены на основе обшитого стальными панелями алюминиевого каркаса, в котором размещена ванна и устройство пневмоавтоматики. Держатель плат перемещается в вертикальном направлении с помощью воздушно-маслянного пневмоцилиндра, обеспечивающего плавность хода. В комплект поставки установки входит вентиляционный канал, система рециркуляции с насосом и сливом, а также ванна из нержавеющей стали.
Установка DS101 дополнительно оснащена системой контроля вязкости материала влагозащитного покрытия, колпаком и вентиляционным патрубком для вытяжки паров растворителя.
Также влагозащиту можно осуществлять и вручную, с использованием кисти.
1.8 Визуальный контроль
- Безокулярный стереомикроскоп LYNX.
Безокулярный стереомикроскоп Lynx с трансфокатором пользуется наибольшим спросом на рынке. Стереоскопическая безокулярная система визуального контроля LYNX позволяет оператору производить контроль намного эффективнее, чем с традиционными окулярными системами за счёт значительного снижения утомляемости зрения, а также повышения уровня свободы положения головы. Оператор имеет возможность работать в очках или контактных линзах.
Стандартная система комплектуется объективами кратностью 0,7х или 1,0х, что позволяет получить максимальное суммарное увеличение системы 28х и 40х соответственно. Наличие дополнительных объективов и умножителей позволяет повысить суммарное увеличение системы до 160 крат с различными рабочими расстояниями.
Модульная конструкция микроскопа позволяет пользователю выбирать между универсальным штативом с дополнительным предметным столиком и монтажным кронштейном. Широкий выбор дополнительных устройств, включая различные системы освещения, возможность подключения фотоаппаратов и цифровых камер позволяет конфигурировать микроскоп под различные задачи инспекции.
Рисунок 1.18 - Безокулярный стереомикроскоп LYNX
Особенности:
- эргономичная конструкция, максимальная свобода движений оператора;
- повышенная производительность, улучшенное выявление дефектов;
- высокие яркость, контрастность и разрешение изображения;
- диапазон увеличений системы 3х - 160x;
- большой диапазон рабочих расстояний.
2 АНАЛИЗ ТЕХНОЛОГИЧНОСТИ КОНСТРУКЦИИ ИЗДЕЛИЯ
2.1 Анализ технологичности
Конструкция печатного узла состоит из печатной платы и установленных на ней элементов. Размер печатной платы 60х60. Стороны соединяются с помощью переходных металлизированных отверстий.
Таблица 2.1 – Показатели технологичности печатного узла
Показатели технологичности печатного узла | Обозначение | Значение |
общее количество монтажных соединений | HM | 155 |
количество монтажных соединений ИЭТ, которые предусматривается осуществить автоматизированным или механизированным способом | Hам | 153 |
общее число ИЭТ, которые должны подготавливаться к монтажу шт., | HпИЭТ | 3 |
количество ИЭТ, шт., подготовка выводов которых осуществляется с помощью полуавтоматов и автоматов | HмпИЭТ | 4 |
количество типоразмеров заимствованных деталей и сборочных единиц | Dтз | 0 |
общее количество типоразмеров деталей и сборочных единиц | Dт | 1 |
общее число элементов замененных микросхемами и микросборками |
Hэмс | 0 |
общее число ИЭТ, шт., не вошедших в МС | HИЭТ | 28 |
число типоразмеров печатных плат | DтПП | 1 |
общее количество печатных плат | DПП | 1 |
Всего деталей | Д | 1 |
Всего сборочных единиц | Е | 1 |
детали и сборочные единицы изготовленные по типовым ТП | Дтп, Етп | 1 |
общее количество операций регулировки и контроля |
Hрк | 3 |
число операций контроля и настройки, выполняемых на полуавтоматических и автоматических стендах | Hарк | 1 |
Коэффициент автоматизации и механизации монтажа:
(2.1)
Коэффициент автоматизации и механизации подготовки ИЭТ к монтажу:
(2.2)
Коэффициент освоенности деталей и сборочных единиц:
(2.3)
Коэффициент применения микросхем и микросборок:
(2.4)
Коэффициент повторяемости печатных плат:
(2.5)
Коэффициент применения типовых технологических процессов:
(2.6)
Коэффициент автоматизации и механизации регулировки и контроля:
(2.7)
Комплексный показатель технологичности:
(2.8)
Таблица 2.2 – Показатели технологичности радиотехнических устройств
qi | i | Коэффициенты | Обозначение | Значение |
1 | 1 | автоматизации имеханизации монтажа | Кам | 0,98 |
2 | 0,8 | автоматизации и механизации подготовки ИЭТ к монтажу | КмпИЭТ | 0,75 |
3 | 0.8 | освоенности деталей и сборочных единиц | Косв | 0 |
4 | 0.5 | применения микросхем и микросборок | Кмс | 0 |
5 | 0.3 | Повторяемостипечатных плат | КповПП | 0 |
6 | 0.2 | Применениятиповых ТП | Ктп | 1 |
7 | 0.5 | автоматизации и механизации регулировки и контроля | Карк | 0,33 |
Комплексный показатель технологичности | К | 0,71 |
Так как комплексный показатель технологичности удовлетворяет заданному по условию (не менее 0,7), то дополнительных мероприятий по повышению технологичности изделия проводить не следует.
2.2 Анализ конструкции
Материалом для печатной платы выбран фольгированный стеклотекстолит СФ-2-35Г-1.5 ГОСТ 10316-78, обладающий высокими электрическими и диэлектрическими свойствами, высокой температурой отслаивания фольги, широким диапазоном рабочих температур, низким (от 0,2 до 0,8%) водопоглащением, высокими значениями объёмного и поверхностного сопротивления, стойкостью к короблению.
Основные свойства СФ-2-35Г-1.5:
- диапазон рабочих температур, °С от –60 до +150;
- удельное объемное сопротивление, Ом*см 5*102 ;
- водопоглощение, % от 0,2 до 0,8;
- сцепления фольги с основанием, Н/м 10.
Согласно техническим требованиям к сборке и монтажу пайку волной необходимо производить припоем ПОС-61 ГОСТ 21931-76, а пайку чип-элементов оплавлением паяльной пасты ПЛ-111 АУЭО.033.012 ТУ.
Основные свойства ПОС-61:
- температура плавления, °С 190;
- теплоемкость, Вт/мк 50,24;
- плотность, кг/м3 8500;
- удельное электрическое сопротивление, Ом*м 0,139*10-6 .
Основные свойства ПЛ-111:
- размер порошка 40-100 мкм;
- растекание пасты, при нанесении и оплавлении, не более 150 мкм;
- клеящая способность не менее 400н/м2 ;
- адгезивная прочность не менее 5*106 н/м2 ;
- средний срок сохранения пасты 3 мес.;
- срок сохранения компонентов 12 мес.
Поставляется в виде 2 компонентов: порошок припоя и органическое связующее. Перед применением компоненты смешиваются в необходимом количестве.
Характеристика элементной базы приведена в таблице 2.3.
Таблица 2.3 – Характеристика элементной базы
Элементы | Габаритные размеры, мм | Масса, г |
Количество, шт | Занимаемая площадь одного, мм2 | Занимаемый объём, мм3 |
ЧИП - резисторы | 1х0,5х0,5 | 0,5 | 11 | 0,5 | 0,25 |
Конденсаторы неполярные 1206 | 3,2х1,6х1,5 | 0,5 | 2 | 5,12 | 7,7 |
Конденсаторы неполярные 1210 | 3,2х2,5х1,65 | 0,6 | 8 | 8 | 13,2 |
Конденсаторы электролитические | 3,5х2,8х1,9 | 1,0 | 2 | 9,8 | 18,6 |
Конденсаторы электролитические | 6,0х3,2х2,6 | 2,0 | 1 | 19,2 | 49,9 |
Светодиод | 5х6 | 0,5 | 2 | 19,6 | 117,7 |
Дроссель | 4,2х3,2х3,2 | 1,0 | 1 | 14,4 | 46,1 |
Кварцевый резонатор | 11,4х4,5х5 | 2.0 | 1 | 55.4 | 277.0 |
Микроконтроллер AT90S4433-BP1 | 37х6,5х5 | 15,0 | 1 | 240,5 | 1202,5 |
Микросхема MAX202CPE | 7,9х6,3х2 | 5,0 | 1 | 49,7 | 99,5 |
Микросхема MAX4541CPA | 3х3х1,5 | 1,5 | 1 | 9 | 13,5 |
Микросхема КР1446УД1А | 5х4х1,75 | 5,0 | 1 | 20,0 | 35,0 |
Микросхема REF02BP | 5х4х1,75 | 5,0 | 1 | 20,0 | 35,0 |
Микросхема КР1157ЕН1 |
4х4х5 | 4,0 | 1 | 16 | 80 |
Разъем PLD-2 | 5х3х8 | 1,0 | 5 | 15 | 120 |
Разъем DBR-9F | 30х18,2х12,6 | 15,0 | 1 | 546 | 6879,6 |
3 Разработка технологической схемы сборки
Технологическим процессом сборки называют совокупность операций, в результате которых детали соединяются в сборочные единицы, блоки, стойки, системы и изделия [5].
Технологическая схема сборки является одним из основных документов, составляемых при разработке технологического процесса сборки. При разработке схемы сборочного состава руководствуются следующими принципами [5]:
- схема составляется независимо от программы выпуска изделия на основе сборочных чертежей, электрической и кинематической схем изделия;
- сборочные единицы образуются при условии независимости их сборки, транспортирования и контроля;
- минимальное числа деталей, необходимое для образования сборочной единицы первой ступени сборки, должно быть равно двум;
- минимальное число деталей, присоединяемых к сборочной единице данной группы для образования сборочного элемента следующей ступени, должно быть равно единице;
- схема сборочного состава строится при условии образования наибольшего числа сборочных единиц;
- схема должна обладать свойством непрерывности, т.е. каждая последующая ступень сборки не может быть осуществлена без предыдущей [4].
Правильно выбранная схема сборочного состава позволяет установить рациональный порядок комплектования сборочных единиц и изделия в процессе сборки. При переходе от схемы сборочного состава к технологической схеме сборки и расположении операций во времени необходимо учитывать следующее [4]:
- вачале выполняются те операции ТП, которые требуют больших механических усилий и неразъемных соединений;
- активные ЭРЭ устанавливают после пассивных;
- при наличии малогабаритных и крупногабаритных ЭРЭ, в первую очередь устанавливаются малогабаритные ЭРЭ;
- заканчивается сборочный процесс установкой деталей подвижных соединений и ЭРЭ, которые используются в дальнейшем для регулировки;
- контрольные операции вводят в ТП после наиболее сложных сборочных операций и при наличии законченного сборочного элемента;
- в маршрутный технологический процесс вводят также те операции, которые непосредственно не вытекают из схемы сборочного состава, но их необходимость определяется техническими требованиями к сборочным единицам.
В качестве основы для технологической схемы сборки платы системы сбора и обработки данных можно выбрать схему сборки с базовой деталью. Такое решение обусловлено наличием базовой детали, поверхности которой будут впоследствии использованы при установке в готовое изделие. Базовой деталью в данном случае является печатная плата. На нее поочередно устанавливаются ИЭТ.
Технологический процесс сборки платы системы сбора и обработки данных состоит из следующих последовательно выполняемых операций:
- дозировка и нанесение на плату паяльной пасты;
- установка поверхностно-монтируемых элементов на плату;
- пайка оплавлением в печи;
- контроль результатов пайки;
- установка на плату элементов навесного монтажа;
- пайка волной припоя;
- маркировка и контроль пайки;
- контроль функционирования блока;
- покрытие платы лаком;
(Технологическая схема сборки представлена в приложении Б).
4 Анализ вариантов маршрутной технологии, выбор технологического оборудования и проектирование технологического процесса
4.1 Анализ вариантов маршрутной технологии
Проектирование техпроцессов сборки и монтажа РЭА начинается с изучения на всех производственных уровнях исходных данных, к которым относятся: краткое описание функционального назначения изделия, технические условия и требования, комплект конструкторской документации, программа и плановые сроки выпуска, руководящий технический, нормативный и справочный материал. К этим данным добавляются условия, в которых предполагается изготавливать изделия: новое или действующее предприятие, имеющееся на нем оборудование и возможности приобретения нового, кооперирование с другими предприятиями, обеспечение материалами и комплектующими изделиями. В результате проведенного анализа разрабатывается план технологической подготовки и запуска изделия в производство.
В разработку ТП сборки и монтажа входит следующий комплекс взаимосвязанных работ:
1. Выбор возможного типового или группового ТП и (при необходимости) его доработка.
2. Составление маршрута ТП общей сборки и установление технологических требований к входящим сборочным единицам.
3. Составление маршрутов ТП сборки блоков (сборочных единиц) и установление технологических требований к входящим в них сборочным единицам и деталям.
4. Определение необходимого технологического оборудования, оснастки, средств механизации и автоматизации.
5. Разбивка ТП на элементы.
6. Расчет и назначение технологических режимов, техническое нормирование работ и определение квалификации рабочих.
7. Разработка ТП и выбор средств контроля, настройки и регулирования.
8. Выдача технического задания на проектирование и изготовление специальной технологической оснастки.
9. Расчет и проектирование поточной линии, участка серийной сборки или гибкой производственной системы, составление планировок и разработка операций перемещения изделий и отходов производства.
10. Выбор и назначение внутрицеховых подъемно-транспортных средств, организация комплектовочной площадки.
11. Оформление технологической документации на процесс и ее утверждение.
12. Выпуск опытной партии.
13. Корректировка документации по результатам испытаний опытной партии.
При разработке маршрутной технологии следует руководствоваться следующим:
- при поточной сборке разбивка процесса на операции определяется ритмом сборки, причем время, затрачиваемое на выполнение каждой операции, должно быть равно или кратно ритму;
- предшествующие операции не должны затруднять выполнение последующих;
- на каждом рабочем месте должна выполняться однородная по характеру и технологически законченная работа;
- после наиболее ответственных операций сборки, а также после регулировки или наладки предусматривают контрольные операции;
- применяются более совершенные формы организации производства - непрерывные и групповые поточные линии и участки гибкого автоматизированного производства (ГАП);
При разработке вариантов маршрутной технологии были учтены существующие типовые процессы сборки и монтажа узла РЭА на печатных платах, которые включают в себя следующие операции:
1. Подготовка поверхности ПП. Включает в себя расконсервацию печатной платы после хранения и визуальную проверку ее поверхности на отсутствие дефектов (обрывы проводников, отслаивание фольги, непротравы, дефекты диэлектрика и т.д.).
2. Подготовка ИЭТ к монтажу.
2.1. Распаковка из первичной тары поставщика.
2.2. Входной контроль. Контроль заключается в проверке поступающих комплектующих по параметрам, определяющим их работоспособность и надежность перед включением этих элементов в производство. В данном случае в виду применения современной надежной элементной базы достаточным будет использование визуального контроля ИЭТ на отсутствие внешних дефектов (сколов, трещин, царапин и т.д.).
2.3. Формовка выводов – это операция гибки выводов электрорадиоизделий для придания им конфигурации, определяющей положение корпуса элемента относительно печатной платы.
2.4. Обрезка выводов. С завода–изготовителя ЭРИ приходят с удлиненными выводами. Обрезать их в соответствии с чертежом можно на разных этапах технологического процесса: сразу же после формовки, перед формовкой или, например, после сборки компонентов на ПП (этот вариант обеспечивает групповую обработку).
2.5. Лужение выводов. Поверхностно-монтируемые элементы, имеющие луженые выводы и поставляемые в упаковке (лента), в данной операции не нуждаются. Лужение выводов требуется для компонентов, монтируемых в отверстия.
3. Комплектование групп - заключается в доставке на рабочие места необходимого количества ЭРИ перед монтажом.
4. Нанесение паяльной пасты. Паяльную пасту можно наносить через трафарет и через специальные дозаторы. В нашем случае пасту наносим трафаретной печатью.
5. Установка элементов в SMD исполнении. Производится с помощью оборудования автоматической установки компонентов.
6. Пайка поверхностно-монтируемых элементов осуществляется оплавлением припоя в конвейерной печи индукционного нагрева.
7. Контроль пайки. Выявление дефектов паяных соединений может производиться визуальным осмотром или с помощью таких способов, как тепловой контроль, контроль по току, рентгенотелевизионный контроль и др. В нашем случае проверка будет производиться визуально.
8. Сборка компонентов, устанавливаемых в отверстия на ПП. Состоит из подачи их к месту установки, ориентации выводов относительно монтажных отверстий или контактных площадок, сопряжением со сборочными элементами и фиксации в требуемом положении. Фиксация может производиться подгибкой выводов после их введения в монтажные отверстия, а также легкоплавкими жидкостями - припоем или органическим составом. Развитие элементной базы потребовало в отдельных случаях введение приклейки компонентов, так как в условиях механических воздействий прочность паяных соединений, выводов элементов может оказаться недостаточной для удержания компонентов на ПП. Все монтируемые элементы фиксируются подгибкой выводов.
9. Пайка компонентов, устанавливаемых в отверстия на ПП. Будет производиться волной припоя на установке пайки волной.
10. Контроль пайки.
11. Выходной контроль печатного узла. На данной операции выявляют различные внешние дефекты и контролируют параметры изделий с помощью КИП или на специальных стендах.
12. Маркирование печатного узла.
13. Лакирование печатного узла. Лакирование осуществляется с целью защиты материала печатной платы, печатных проводников и компонентов от воздействия окружающей среды нанесением лака при помощи кисти.
Отдельные сборочно-монтажные операции, а также значения оперативного и вспомогательного времени на их выполнение приведены в таблице 4.1 и 4.2.
Значения оперативного и вспомогательного времени определяются, с помощью справочных материалов [7].
Проведем анализ двух вариантов маршрутной технологии сборки и монтажа изделия и выберем наиболее оптимальный.
Таблица 4.1 – Первый вариант маршрутной технологии
Последовательность операций |
Оборудование оснастка | 1 ВАРИАНТ | |||
n | Tоп | nTоп | Тпзсм | ||
Расконсервация и контроль ПП | Монтажный стол СМ-З |
1 | 0,637 | 0,637 | - |
Распаковка и проверка ЭРЭ (на 100 шт.) на ленте россыпью |
Монтажный стол СМ-З |
- | |||
24 | 0,06 | 0,144 | |||
20 | 0,027 | 0,054 | |||
Подготовка выводов компонентов | Автоматическая система обрезки и формовки выводов CompactLine | 3 | 0,04 | 0,12 | 30 |
1 | 0,02 | 0,02 | 30 | ||
Комплектование элементов по операциям |
Монтажный стол СМ-З |
1 | 0,5 | 0,5 | - |
Нанесение паяльной пасты на автомате |
Автоматический трафаретный принтер Exerra EP20 | 1 | 0,6 | 0,6 | 30 |
Установка SMD компонентов автоматом |
Автомат установки SMD компонентов MYDATA серии MY | 29 | 0,025 | 0,725 | 30 |
Пайка оплавлением припоя | Конвекционная печь Heller серии Mark III | 1 | 0,7 | 0,7 | 30 |
Контроль пайки | Визуальный контроль | 1 | 0,207 | 0,207 | - |
Установка выводных компонентов | Монтажная станция Royonic 550 | 13 | 0,05 | 0,65 | 30 |
1 | 0,064 | 0,064 | 30 | ||
Пайка волной припоя | Система пайки волной припоя ELECTROVERT VectraElite | 1 | 0,78 | 0,78 | 50 |
Контроль пайки | Визуальный контроль | 1 | 0,207 | 0,207 | - |
Отмывка плат после пайки | Ультразвуковая установка отмывки BlO-Chem G13935 | 1 | 0,41 | 0,41 | 20 |
Маркирование | Трафарет, кисть | 1 | 0,4 | 0,4 | - |
Выходной контроль |
Стенд автоматизированного контроля | 1 | 0,5 | 0,5 | 15 |
Герметизация | Установка влагозащиты погружением DS101 | 1 | 0,5 | 0,5 | 20 |
ИТОГО | 9,15 | 295 |
Таблица 4.2 – Второй вариант маршрутной технологии
Последовательностьопераций | Оборудование оснастка | 1 ВАРИАНТ | |||
n | Tоп | nTоп | Тпзсм | ||
Расконсервация и контроль ПП | Монтажный стол СМ-З |
1 | 0,637 | 0,637 | - |
Распаковка и проверка ЭРЭ (на 100 шт.) на ленте россыпью |
Монтажный стол СМ-З |
- | |||
24 | 0,06 | 1,44 | |||
20 | 0,027 | 0,54 | |||
Подготовка выводов компонентов: аксиальных радиальных |
Формовка выводов пинцетом | 2 | 0,036 | 0,072 | 5 |
1 | 0,036 | 0,036 | 5 | ||
Комплектованиеэлементов по операциям | Монтажный стол СМ-З |
1 | 0,5 | 0,5 | - |
Нанесение паяльной пасты на автомате |
Трафаретный принтер UNIPRINT | 1 | 0,2 | 0,2 | 20 |
Установка SMD компонентов | Полуавтомат MM500 | 29 | 0,14 | 4,06 | 20 |
Пайка оплавлением припоя | Печь оплавления SEF Roboter настольного типа 548.04 G | 1 | 0,9 | 0,9 | 20 |
Контроль пайки | Визуальный контроль | 1 | 0,207 | 0,207 | - |
Установка выводных компонентов | Монтажная станция Royonic 550 | 13 | 0,05 | 0,65 | 30 |
1 | 0,064 | 0,064 | 30 | ||
Пайка волной припоя | Система пайки волной припоя ELECTROVERT VectraElite | 1 | 0,78 | 0,78 | 50 |
Контроль пайки | Визуальный контроль | 1 | 0,207 | 0,207 | - |
Маркирование | Трафарет, кисть | 1 | 0,4 | 0,4 | - |
Выходной контроль | Стенд автоматизированного контроля | 1 | 0,5 | 0,5 | 15 |
Герметизация | Кисть | 1 | 1 | 1 | 20 |
Сушка | Сушильный шкаф | 1 | 1 | 1 | 2,5 |
ИТОГО | 14,193 | 217,5 |
Тип производства можно определить исходя из объема партии. В нашем случае тип производства – крупносерийное (N=700 тыс. шт.) [6].
4.2 Выбор оптимального варианта по производительности
Выбор оптимального варианта технологического процесса необходимо обосновать производительностью труда. Производительность – количество деталей в штуках, которое изготовлено за единицу времени. Для этого проводится техническое нормирование операций технологического процесса.
Полное время, затрачиваемое на выполнение одной операции, называется штучно-калькуляционным временем [5]:
![]() |
(4.1) |
где – подготовительно-заключительное время, которое затрачивается на ознакомление с чертежами, получение инструмента, подготовку и наладку оборудования и выдается на всю программу выпуска.
![]() |
(4.2) |
где – основное время (время работы оборудования);
– вспомогательное время (время на установку и снятие детали);
– время обслуживания (время обслуживания и замены инструмента);
– время перерывов (время на регламентированные перерывы в работе).
Для сборочно-монтажного производства объединяют и
и получают оперативное время
, а
составляют дополнительное время и задают его в процентах от
в качестве коэффициентов.
Тогда:
![]() |
(4.3) |
где – коэффициент, зависящий от группы сложности аппаратуры и типа производства;
– коэффициент, учитывающий подготовительно-заключительное время и время обслуживания;
– коэффициент, учитывающий долю времени на перерывы в работе
Таблица 4.3 – Значение коэффициентов ,
,
[5]
К1 | 1,12 |
К2 | 5,4 |
К3 | 5 |
![]() |
![]() |
Составляется два уравнения для вычисления суммарного штучно-калькуляционного времени:
![]() |
(4.4) |
![]() |
(4.5) |
где и
– число операций по одному и второму варианту соответственно.
Подготовительно – заключительное время определяется по формуле:
![]() |
(4.6) |
где – сменная норма подготовительно – заключительного времени.
![]() |
![]() |
![]() |
![]() |
Рассчитывается критический размер партии:
![]() |
(4.7) |
При программе выпуска более 7873 штуки за плановый период с двухсменной работой эффективнее будет первый вариант.
Чем ближе размер критической партии к программе выпуска, тем меньше разница между сравниваемыми вариантами технологических процессов.
Наблюдается незначительная разница между временем для двух вариантов, однако Тшт-к
первого варианта меньше, чем второго.
Следовательно, для варианта с большим уровнем автоматизации единовременные затраты будут выше, но текущие затраты меньше вследствие повышения производительности и снижения квалификации рабочих. Поэтому предпочтительнее будет первый вариант.
Для определения количества устанавливаемых ЭРЭ и ИМС на платы в ходе выполнения i – й операции необходим расчет ритма, который производится по формуле
(4.8)
где: – расчетная программа выпуска, определяется по формуле
(4.9)
где – плановая программа выпуска,
= 700000 шт.;
– возможные технологические потери, %; ( = 2).
- действительный фонд времени за плановый период, определяется по формуле
(4.10)
где Д – число дней за плановый период, Д = 256 дней;
s – число смен, s = 2;
t – продолжительность смены в часах, t = 8 часов;
– коэффициент, учитывающий время регламентированных перерывов в работе линии (0,94 – 0,95).
4.3 Выбор технологического оборудования
Выбор технологического оборудования согласно ГОСТ 14.304-73 ЕСТПП проводится путем анализа затрат на реализацию технологического процесса в установленный промежуток времени при заданном качестве изделия.
Выбор оборудования проводят также по главному параметру, являющемуся наиболее показательным для выбираемого оборудования, т.е. в наибольшей степени выявляющему его функциональное значение и технические возможности. В качестве главного параметра часто берут производительность технологического оборудования.
Основные параметры используемого оборудования приведены в разделе 1. Перечислим их еще раз:
Для обрезки и формовки выводов будет использоваться высокопроизводительная автоматическая система CompactLine. Она предназначена для автоматической обрезки и формовки выводов для всех существующих на сегодняшний день типов корпусов. Система Compact Line™ оснащена высокоскоростным прессом для обрезки и формовки, имеет возможность смены магазинов в момент выполнения рабочего цикла, отсева неверно сориентированных изделий без остановки процесса, функцией быстрой смены инструмента и оснастки. Специальная конструкция системы Compact Line™ позволяет свести к минимуму время на плановый ремонт и обслуживание, а простота программного обеспечения и интерфейса управления в целом позволяют отказаться от углубленного обучения операторов, ведь машина не требует вмешательства человека даже в случае ошибки ориентации рамок. Загрузка и выгрузка изделий - это все, что выполняет оператор.
Нанесение паяльной пасты осуществляется на автоматическом трафаретном принтере Exerra EP20. Принтер MOTOPRINT-AVL с автоматической системой центрирования разработан для универсальной и точной трафаретной печати паяльной пасты, клея для поверхностного монтажа и других материалов для серийного производства. Exerra EP20 обладает следующими достоинствами:
- устойчивая монолитная станина с гранитным рабочим столом;
- управление силой давления ракелей с обратной связью;
- управление работой всех осей сервомоторами с оптической связью;
- высокоточное совмещение трафарета и платы;
- дружественный пользовательский интерфейс;
- мощная система 2D-контроля качества нанесения паяльной пасты и засорения апертур трафарета;
- автоматическая система очистки трафарета.
Установка SMD компонентов будет производиться автоматом установки MYDATA серии MY. Автоматы MYDATA (Швеция) являются одними из признанных лидеров в точности и скорости перехода с одного изделия на другое. Скорость заправки современных питателей от MYDATA исчисляется секундами. Сокращение времени простоя приводит к тому, что при равных скоростных характеристиках, указанных по IPC 9850, в конце рабочей смены линия с автоматом MYDATA выпускает на 20-50% большее количество продукции. Высокая точность позволяет автоматам MYDATA осуществлять сборку, соответствующую самым жестким современным требованиям. Установщик типа MY9 обеспечивает общую емкость питателей в 96 восьмимиллиметровых лент с компонентами, а установщики MY12, MY15 и MY19 обеспечивают общие емкости в 144, 192 и 256 лент соответственно (при установке сборочных столов, занимающих 3 места). При этом при заказе машин с большими сборочными столами максимальное количество питателей может уменьшиться. Во всех установщиках, производимых MYDATA, питатели установлены со стороны оператора машины. Еще одна особенность машин – раздельное перемещение по осям, что в сочетании с высокопрочной цельной станиной обеспечивает очень стабильное и точное позиционирование монтажного модуля. Благодаря тому, что все питатели электронные и с линейным приводом, воздух необходим только для захвата и монтажа компонентов. Его потребность обеспечивает встроенная в машину помпа.
На конвейерной печи конвекционного нагрева Heller серии Mark III будет производиться пайка оплавлением припоя. Особенностью серии является новый увеличенный туннель нагрева собственной разработки. Туннель имеет бесперегородочную конструкцию, что улучшает стабильность и повторяемость результатов, как от зоны к зоне, так и от печи к печи. Конструкция туннеля обеспечивает большую гибкость при транспортировке плат, более жесткую конструкцию и более изящный внешний вид самой печи.
Для установки элементов, монтируемых в отверстия, будет использоваться монтажная станция Royonic 550 (Royonic, Германия). Сборочные места фирмы Royonic позволяют быстро и качественно выполнить сборку печатной платы. Модель 550 имеет высокоскоростную систему подачи многопарных ячеек, в которых находятся компоненты. Запатентованная система подачи обеспечивает доступ к любой ячейке в любой последовательности. Система обеспечивает доступ к ячейкам от одной до восьми одновременно. Установка идеально подходит как для сборки плат в крупносерийном производстве, так и для ремонта плат.
Элементы, монтируемые в отверстия, будут паяться волной припоя на установке ELECTROVERT VectraElite. Особенности системы:
- работа по свинцовой и бессвинцовой технологии;
- системы спрей-флюсователей: ServoSpray™, Performa™, ServoJet™ и Optima™;
- насадки UltraFill™ для работы по бессвинцовой технологии;
- высокоскоростной конвекционный HVC преднагрев сверху для оптимизации производительности;
- ширина платы - до 508 мм;
- длина зоны предварительного нагрева - до 1,8 м.
Отмывка платы будет производиться на ультразвуковой установке отмывки BlO-Chem G13935. Ультразвуковые системы BlO-Chem предназначены для очистки печатных плат, компонентов, металлических изделий от остатков всевозможных химических материалов применяемых в соответствии с технологией обработки. Устройства сделаны из устойчивого к коррозии материала и могут применяться для работы с любыми невзрывоопасными жидкостями.
УЗ-генератор может работать в трех режимах:
а). амплитудное колебание мощности УЗ с частотой 0,5 с;
б). УЗ-пульсация с частотой 0,5 с;
в). постоянная частота без изменения интенсивности (35кГц).
Установка имеет удобный слив жидкости через специальное технологическое отверстие. Пульт управления устройством очень прост в работе и не требует специальных навыков оператора.
Герметизация печатной паты будет производиться на установке влагозащиты погружением DS101.
Установка влагозащиты DS101 предназначена для прецизионного нанесения влагозащитных покрытий на печатные узлы методом их погружения в ванну с материалом покрытия. DS101 ориентирована на применение в серийном производстве.
Важным показателем правильности выбора технологического оборудования является коэффициент загрузки и использование оборудования по основному времени, который определяется как отношение расчетного количества единиц оборудования по данной операции к принятому (фактическому) количеству
:
![]() |
(4.11) |
Расчетное количество единиц оборудования (рабочих мест) определяется как отношение штучного времени данной операции к ритму выпуска r:
![]() |
(4.12) |
Полученные результаты сведем в таблицу 4.4.
Таблица 4.4 – Значение коэффициентов загрузки оборудования
№ | Технологическое оборудование |
Значение штучного времени ![]() |
Значение коэффициента ![]() |
Значение коэффициента ![]() |
Значение коэффициента ![]() |
1 | Автоматический трафаретный принтер Exerra EP20 | 0,49 | 1,5 | 2 | 0,75 |
2 | Автомат установки SMD компонентов MYDATA серии MY | 0,9 | 2,72 | 3 | 0,9 |
3 | Конвейерная печь Heller серии Mark III | 0,618 | 1,87 | 2 | 0,93 |
4 | Автоматическая система обрезки и формовки выводов CompactLine | 0,124 | 0,375 | 1 | 0,375 |
5 | Монтажная станция Royonic 550 | 0,88 | 2,68 | 3 | 0,89 |
6 | Установка пайки ELECTROVERT VectraElite | 0,96 | 2,92 | 3 | 0,97 |
7 | Ультразвуковая установка отмывки BlO-Chem G13935 | 0,5 | 1,5 | 2 | 0,75 |
8 | Стенд автоматизированного контроля УТС-9042 | 0,62 | 1,8 | 2 | 0,9 |
9 | Установка влагозащиты погружением DS101 | 0,62 | 1,8 | 2 | 0,9 |
По полученным результатам построим график загрузки оборудования.
|

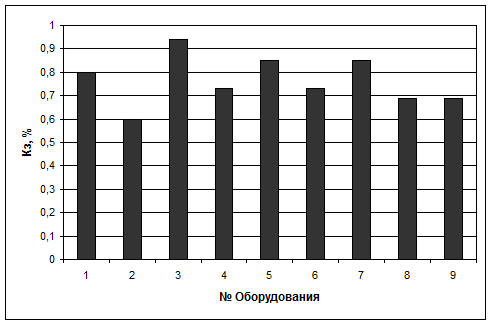
Рисунок 4.1 – График загрузки оборудования
Среднее значение коэффициента загрузки оборудования равно Кз.ср = 0,76, что соответствует нормативному значению для серийного производства, для которого Кз 0,75 – 0,85.
4.4 Разработка маршрутно–операционной технологии
После установления маршрута сборки и монтажа печатного узла дадим описание каждой операции с указанием технологического оснащения, режимов проведения и норм расхода материалов [5, 6, 8].
1. Расконсервация и контроль печатной платы.
Извлечь печатную плату из тары поставщика. Промыть печатную плату при помощи кисти от консервирующего покрытия в ванне со спирто–нефрасовой смесью. Контролировать визуально поверхность печатной платы на отсутствие дефектов (отслоение дорожек, расслоение диэлектрика, непротравы). При наличии дефектов плату отложить в тару с надписью Брак. Проверенную плату положить в тару АЮР 7877–4048.
Средства технологического оснащения:
- стол монтажный СМ-З;
- вытяжной шкаф 2Ш-ИЖ;
- ванна цеховая 92.АЮР.53.003;
- кисть КХФК №10 ТУ 17-15-07-89;
- пинцет 92.7872–1374 ОСТ 92-3890-85;
- безокулярный стереомикроскоп LYNX;
- тара АЮР 7877–4048
Расход спирто-нефрасовой смеси:
- 0,00024 л/плату (площадь промывки S=4800мм2 , норма расхода – 0,05л/м2 );
Расход кисти:
- 0,0005 шт./плату (норма расхода 0,1 кисти/м2 ).
Суммарное оперативное время Топ = 0,637 мин.
2. Распаковка и контроль ИЭТ. Извлечь ИЭТ из тары поставщика, произвести визуальный контроль на целостность корпусов и выводов, отсутствие внешних дефектов (трещин, сколов). Годные элементы разложить в тару по типономиналу. Отбраковать поврежденные ИЭТ в тару с надписью Брак.
Средства технологического оснащения:
- стол монтажный СМ-З;
- тара АЮР 7877– 4048;
- пинцет ППМ 120 РД 107.290.600.034-89;
- безокулярный стереомикроскоп LYNX;.
Суммарное оперативное время Топ = 0,198 мин.
3. Подготовка выводов ИЭТ, монтируемых в отверстия. Формовка и обрезка выводов производиться с использованием автоматической системы CompactLine. Извлечь навесные компоненты из тары и поместить в магазины системы формовки и обрезки. После проведения операции уложить компоненты в тару АЮР 7877–4048.
Средства технологического оснащения:
- автоматическая система формовки и обрезки выводов CompactLine;
- тара АЮР 7877–4048;
- пинцет ППМ 120 РД 107.290.600.034-89.
Суммарное оперативное время: Топ = 0,14 мин.
4. Комплектование групп.
Комплектовать группы ИЭТ для сборки согласно спецификации СПН.446126.013. Элементы с аксиальными и радиальными выводами укладываются в кассеты, поставляемые вместе с установкой Royonic 550, остальные – на ленты, которые потом подаются на автомат установки SMD компонентов MYDATA серии MY. Произвести доставку укомплектованных групп на рабочие места.
Средства технологического оснащения:
- стол монтажный СМ-З,
- пинцет ППМ 120 РД 107.290.600.034-89,
- тара АЮР 7877–4048.
Суммарное оперативное время Топ = 0,5 мин.
5. Нанесение паяльной пасты. Извлечь приготовленные печатные платы из тары, установить плату в автоматический трафаретный принтер Exerra EP20. Установить трафарет. Нанести на поверхность печатной платы паяльную пасту ПЛ–111. После нанесения паяльной пасты, извлечь плату из установки. Трафарет после нанесения пасты промыть деионизованной водой в ванне и просушить.
Средства технологического оснащения:
- автоматический трафаретный принтер MOTOPRINT-AVL;
- трафарет СПН.446126.013;
- ванна цеховая 92.АЮР.53.003
- тара АЮР 7877–4048;
- скорость дозирования 15000 точек/ч.
Расход паяльной пасты ПЛ – 111 АУЭО.033.012 ТУ: 1,02 г/плату (норма расхода 0,03 г/соединение).
Суммарное оперативное время Топ = 0,6 мин.
6. Установка поверхностно – монтируемых компонентов. Установить поверхностно – монтируемые компоненты (поз. 2-15,17-20, 23-35, 38) по заданной программе на автомате MYDATA серии MY. Фиксация элементов осуществляется при помощи паяльной пасты ПЛ – 111.
Средства технологического оснащения:
- автомат MYDATA серии MY;
- тара АЮР 7877-4048.
Суммарное оперативное время Топ = 0,725 мин.
7. Пайка оплавлением припоя. Извлечь платы с установленными поверхностно-монтируемыми компонентами из тары и разместить их на ленте транспортера печи конвейерной печи Heller серии Mark III. Произвести пайку поверхностно-монтируемых компонентов оплавлением. После пайки поместить платы на стол. Поскольку в процессе пайки происходит испарение припоя, установку необходимо подключить к вытяжному шкафу.
Средства технологического оснащения:
- вытяжной шкаф 2Ш-ИЖ;
- Heller серии Mark III;
- тара АЮР 7877 – 4048.
Режимы пайки:
- скорость движения конвейера 800 мм/мин;
- число зон нагрева 4.
Время всего процесса пайки 46 с.
В течении первых 17 с. обеспечить возрастание температуры с 300 С до 1500 С, в течение 6 с. с 1500 С до 1600 С, в течение 15 с. со 1600 С до 1950 С. В течение последних 4 с. температура падает со 1950 С до 1600 С.
Суммарное оперативное время Топ = 0,7 мин.
8. Контроль пайки. Контролировать визуально качество пайки (отсутствие смещения компонентов с контактных площадок, непропаев). Годные платы положить в тару АЮР 7877-4048. Дефектные платы отложить в тару АЮР 7877-4048 с надписью Брак.
Средства технологического оснащения:
- стол монтажный СМ-З;
- безокулярный стереомикроскоп LYNX;
- тара АЮР 7877 – 4048.
Суммарное оперативное время Топ = 0,207 мин.
9. Установка ИЭТ, монтируемых в отверстия. Установить ИЭТ поз. 16, 21, 22, 34-37 по заданной программе на монтажной станции Royonic 550.
Средства технологического оснащения:
- монтажная станция Royonic 550;
- тара АЮР 7877-4048;
- скорость установки до 1600 комп./час
Суммарное оперативное время Топ = 0,714 мин.
10. Пайка волной припоя. Извлечь платы с установленными на них компонентами, монтируемыми в отверстия, из тары и разместить их на ленте транспортера машины пайки волной ELECTROVERT VectraElite. После пайки снять плату с конвейера печи и положить ее в тару.
Средства технологического оснащения:
- вытяжной шкаф 2Ш-ИЖ;
- машинапайкиволной ELECTROVERT VectraElite;
- тара АЮР7877-4048.
Расход припоя ПОС-61 ГОСТ 21931-76: 6,38 г/плату (норма расхода – 0,11г/пайку).
Режимы пайки: скорость движения ленты транспортера 0,5 ± 1,8 м/мин, угол наклона ленты конвейера от 5 до 7°, температура припоя в ванне 260 °С, тип волны - coN2tour.
Суммарное оперативное время Топ = 0,78 мин.
11. Контроль пайки. Контролировать визуально качества пайки (отсутствие перемычек, мостиков из припоя, непропаев). Годные платы положить в тару. В случае невозможности устранения дефектов плату отложить в тару АЮР 7877-4048 с надписью Брак.
Средства технологического оснащения:
- стол монтажный СМ-З;
- паяльник ПВНРС 25-36;
- вытяжной шкаф 2Ш-ИЖ;
- пинцет ППМ 120 РД 107.290.600.034-8;
- тара АЮР7877-4048;
- безокулярный стереомикроскоп LYNX.
Суммарное оперативное время Топ = 0,207 мин.
12. Отмывка. Отмыть печатную плату от остатков флюса на ультразвуковой установке отмывки BlO-Chem G13935.
Средства технологического оснащения:
· вытяжной шкаф 2Ш-ИЖ;
· ультразвуковая установка отмывки BlO-Chem G13935;
· тара АЮР7877-4048.
Температура: 55±10 °С.
Суммарное оперативное время Топ = 0,41 мин.
13. Маркирование. Маркировать согласно СПН.686126.013 СБ заводской номер, дату изготовления кистью. Краска БМ, белая, ТУ 029-02-859-78, шрифт 4 по НО 010.007. В виду наличия паров ЛВЖ предусмотреть вытяжной шкаф.
Средства технологического оснащения:
- стол монтажный СМ-З;
- тара для краски; тара АЮР7877-4048;
- трафарет;
- кисть КХФК №2 ТУ 17-15-07-89;
- вытяжной шкаф 2Ш-ИЖ;
Расход кисти: 0,00432 шт./плату (норма расхода – 0,9/м2 ).
Суммарное оперативное время Топ = 0,4 мин.
14. Выходной контроль печатного узла. Извлечь узел из тары. Произвести визуальный контроль на отсутствие внешних дефектов. Протестировать устройство на автоматизированном стенде. Неисправные узлы отложить в тару с надписью Брак. Годные платы уложить в тару Годные.
Средства технологического оснащения:
- стенд автоматизированного контроля;
- монтажный стол СМЗ;
- тара АЮР 7877-4048.
Суммарное оперативное время Топ = 0,5 мин.
15. Лакирование. Лакировать плату на установке влагозащиты погружением DS101 лаком ФП-525 ТУ 6-10-1553-78. Элементы поз. 36 и 37 от покрытия лаком предохранить липкой лентой.
Средства технологического оснащения:
- установка влагозащиты DS101;
- тара АЮР 7877-4048;
- лента ПВХ15х0,2 голубая, первый сорт, ГОСТ16214-86;
- тара АЮР 7877-4048; тара для ЛВЖ АЮР7877-4074.
Расход лака: 0,192 г/плату (норма расхода – 40г/м2 );
Суммарное оперативное время Топ = 0,50 мин.
После контроля печатную плату уложить в тару и доставить на склад готовой продукции.
Комплект технологической документации на технологический процесс сборки и монтажа блока управления приведен в приложении.
5 ПРОЕКТИРОВАНИЕ УЧАСТКА СБОРКИ И МОНТАЖА
Основным направлением, которое позволяет решить проблему существенного роста производительности труда, является внедрение в производство механизированных, автоматизированных и автоматических поточных линий. Автоматическая линия представляет собой систему автоматических станков и агрегатов, которые устанавливаются в технологической последовательности и объединяются общими системами транспортирования заготовок, удаления отходов и управления.
В зависимости от номенклатуры закрепленных за линией изделий поточные линии могут быть однопредметными и многопредметными. За однопредметной линией закреплена сборка изделий одного наименования, за многопредметной - изделий разных наименований, сходных по конструктивно-технологическим признакам. Так как разработка технологического процесса производится для одного изделия, то проектирование участка сборки и монтажа следует выполнять по методике для однопредметной поточной линии.
Основным оборудованием автоматизированных транспортных систем, в том числе поточно-механизированных линий, являются конвейеры. Выбор типа конвейера зависит от массы и габаритных размеров собираемых деталей, возможности выполнения работ со съемом изделий или без него, наличия параллельных рабочих мест и других факторов.
По конструкции конвейеры для поточных линий делятся на ленточные, пластинчатые, тележечные, роликовые, элеваторы. Так как масса изделия меньше 2 кг, а его габаритные размеры до 80X80 мм, ритм конвейера - менее 5 мин, с наличием рабочих мест дублеров, то правильным будет выбор распределительного пластинчатого вертикально-замкнутого конвейера
Пластинчатые конвейеры применяются в основном для сборки изделий до 40 кг и длиной до 500 мм, а также в том случае, когда предъявляются повышенные требования к точности качеству сборки или механизации съема изделий.
В качестве несущего органа конвейера применяются стальная пластина, которая одновременно выполняет функцию цепи. Пластинчатые конвейеры могут быть распределительными и рабочими, а по расположению в пространстве - только вертикально замкнутыми и в большинстве случаев периодического действия.
Расчет однопредметной непрерывно-поточной линии, выполненной на конвейере, осуществляется следующим образом.
Количество рабочих мест, выполняющих параллельно одну и ту же операцию CPi :
![]() |
(5.1) |
где tOi – норма времени i-ой операции;
r – ритм выпуска изделий (r=0,33).
Результаты расчета количества рабочих мест представлены в таблице 5.1.
Таблица 5.1 – Расчет количества рабочих мест
№ операции | Последовательность операций | Tоп | СPi | nСPi |
1 | Расконсервация и контроль ПП | 0,637 | 1,93 | 2 |
2 | Распаковка и проверка ИЭТ | 0,198 | 0,6 | 1 |
3 | Подготовка выводов ИЭТ | 0,1 | 0,3 | 1 |
4 | Комплектование элементов | 0,5 | 1,51 | 2 |
5 | Нанесение паяльной пасты | 0,6 | 1,8 | 2 |
6 | Установка поверхностно монтируемых компонентов | 0,0725 | 0,2 | 1 |
7 | Пайка оплавлением припоя | 0,7 | 2,3 | 3 |
8 | Контроль пайки | 0,207 | 0,62 | 1 |
9 | Установка ИЭТ | 0,714 | 2,16 | 3 |
10 | Пайка волной припоя | 0,78 | 2,36 | 3 |
11 | Контроль пайки | 0,207 | 0,62 | 1 |
12 | Отмывка плат после пайки | 0,41 | 1,24 | 2 |
13 | Маркирование | 0,4 | 1,2 | 2 |
14 | Выходной контроль печатного узла | 0,5 | 1,5 | 2 |
15 | Лакирование | 0,5 | 1,5 | 2 |
Коэффициент загрузки рабочего места i определяется как отношение расчетного числа рабочих мест к принятому (округленному до целого числа):
![]() |
(5.2) |
где Спрi – принятое число рабочих мест.
Коэффициент i должен находиться в пределах 0,9 i 1,2, иначе необходимо объединять операции.
Для синхронизации объединяем операции 1; 2, 3, 4; 5, 6; 7 и 8; 9; 10, 11, 12; 13; 14; 15.
Результаты расчета количества рабочих мест и коэффициента загрузки рабочих мест представлены в таблице 5.2
Таблица 5.2 – Расчет количества рабочих мест на поточной линии
№ операции |
№ рабочего места | Tоп | СPi | Спр i | Место расположения | i |
1 | 1 | 0,637 | 1,93 | 2 | Вне поточной линии | 0,96 |
2, 3, 4 | 2 | 0,798 | 2,4 | 2 | Вне поточной линии | 1,2 |
5, 6 | 3 | 0,67 | 2 | 2 | Поточная линия | 1 |
7, 8 | 4 | 0,907 | 2,92 | 3 | Поточная линия | 0,97 |
9 | 5 | 0,714 | 2,16 | 2 | Поточная линия | 1,08 |
10, 11, 12 | 6 | 1,39 | 4,2 | 4 | Вне поточной линии | 1,05 |
13 | 7 | 0,4 | 1,2 | 1 | Поточная линия | 1,2 |
14, 15 | 8 | 1 | 3 | 3 | Поточная линия | 1 |
Общее количество рабочих мест на линии:
![]() |
(5.3) |
Из общего количества рабочих мест Кр на поточной линии требуется 11 рабочих, остальные заняты либо во вспомогательном производстве, либо вне линии. Таким образом, число рабочих на поточной линии Кр ’ = 11.
Максимальное количество рабочих мест на участке Kобщ :
![]() |
(5.4) |
где КРЕЗ – количество резервных мест;
KКОМП – количество рабочих мест комплектовщиков;
KКОНТР – количество рабочих мест контролеров.
Принимаем КРЕЗ =4; ККОМП =2; ККОНТР =1;
![]() |
Оптимальным выбором при заданных условиях производства будет являться распределительный пластинчатый вертикально-замкнутый конвейер с ручным съемом изделий периодического характера действия, так как такой конвейер обеспечивает высокое качество сборки изделия.
Размеры пластины. Ширина рассчитывается по формуле:
![]() |
(5.5) |
где bизд - ширина изделия, в мм.
b=60 + 50 =110 (мм)
Определяем длину конвейера по формуле:
(5.6)
где L1 , L2 - длина проводной и натяжной станций соответственно (выбираем по справочным данным, L1 , L2 =1,5 м) [5];
Lp - рабочая длина несущего органа конвейера, определяется по формуле (для двухрядного расположения мест):
![]() |
(5.7) |
где l - расстояние между двумя соседними рабочими местами (с одной стороны конвейера обычно принимается 1,2 – 1,6 м) [4];
Кmax – максимальное количество рабочих мест на линии (18 мест).
(м)
(м)
Количество предметов в заделе NZ :
![]() |
(5.8) |
где Nобор – оборотный задел;
Nрез – резервный задел;
Nтран – транспортный задел;
Nтех – технологический задел.
Оборотный задел равен размеру сменной потребности линии:
![]() |
Резервный задел – 3% от сменного выпуска изделий:
![]() ![]() |
(5.9) |
![]() |
Транспортный задел:
![]() |
(5.10) |
где NТР – количество изделий, транспортируемое в пачке NТР =5.
![]() |
Технологический задел:
![]() |
(5.11) |
![]() |
Подставляя в формулу 5.8 полученные значения, имеем:
![]() ![]() |
Скорость ленты конвейера при непрерывном ее движении
![]() |
(5.12) |
где d – шаг конвейера (расстояние между соседними рабочими местами, на которых выполняются сборочно-монтажные операции), м. В соответствии с нормами на расстояния между рабочими местами с общим рабочим столом d=1,2…1,6 м [6].
Тогда
![]() |
Производительность конвейера определяется по формуле:
![]() |
(5.13) |
где m - масса изделия; m = 0,1 кг;
![]() |
При разработке планировок в зависимости от их назначения должны быть предусмотрены площади для размещения:
- технологического и контрольно-испытательного оборудования;
- обслуживающих подразделений;
- рабочих мест;
- проходов и проездов;
- средств и путей перемещения материалов, изделий и технологических отходов;
- материалов, заготовок, полуфабрикатов и комплектующих изделий;
- готовой продукции;
- вспомогательных помещений.
При разработке планировок должны быть решены следующие задачи:
- обеспечение технологической последовательности выполнения операций;
- создание поточности движения материалов, полуфабрикатов, комплектующих и готовых изделий;
- сокращение расстояний перемещений грузов;
- эффективное использование производственного оборудования, рабочих мест и площадей;
- обеспечение безопасности работы.
Планировки разрабатываются в следующей последовательности:
- сбор исходных данных;
- определение состава и количества технологического оснащения для выполнения технологических операций;
- разработка схем расположения цехов, участков и групп оборудования с технико-экономическим обоснованием вариантов;
- определение рациональной последовательности расстановки оборудования и рабочих мест согласно нормам;
- выполнение чертежа планировки;
- утверждение планировки.
При составлении планировок должны быть учтены следующие требования:
- технологический поток изготовления изделия должен быть непрерывным;
- транспортно-складские работы должны быть максимально механизированы или автоматизированы, и входить в общий технологический поток;
- должна быть обеспечена сохранность материальных ценностей, а также возможность учета деталей, полуфабрикатов и готовых изделий;
- капитальные затраты должны быть оптимальными, а окупаемость оборудования – укладываться в действующие в отрасли нормативы;
- для распределительного конвейера при расположении рабочих столов в шахматном порядке [5]:
- ширина прохода между линиями двух конвейеров, мм не менее 1300;
- ширина прохода между линией и стеной, мм: не менее 1000;
- расстояния между рабочими местами, мм: 1200 – 1600;
- расстояния между рабочими местами и колоннами, мм: 500.
Кроме конвейера используются также следующие напольные транспортные средства тележки – для обеспечения рабочих мест деталями со склада комплектующих и автопогрузчики – для загрузки деталями склада и транспортирования готовой продукции из склада на отгрузку. Следовательно, необходимо предусмотреть ширину проездов и расстояния между рядами оборудования достаточные для передвижения соответствующих транспортных средств: 1200 мм для тележечного транспорта, 2000 мм для автопогрузчиков.
Ориентировочная планировка участка сборки и монтажа приведена в Приложении.
6 Разработка оснастки для сборочно-монтажных работ
Технологическая оснастка представляет собой дополнительные или вспомогательные устройства, предназначенные для реализации технологических возможностей оборудования или работающие автономно на рабочем месте с использованием ручного, пневматического, электромеханического и других приводов. Технологическая оснастка применяется для выполнения следующих операций [6]:
- подготовки выводов радиоэлементов к монтажу (гибка, обрезка, формовка, лужение);
- подготовки проводов и кабелей к монтажу (снятие изоляции, зачистка, заделка, маркировка, вязка жгутов, лужение);
- механосборочных (расклепка, развальцовка, запрессовка, расчеканка, свинчивание, стопорение резьбовых соединений);
- установки радиоэлементов на печатные платы (укладка, закрепление, склеивание);
- монтажных (пайка, сварка, накрутка, демонтаж элементов);
- регулировочных и контрольных операций (подстройка параметров, визуальный и автоматический контроль) и т.д.
Разработка технологической оснастки имеет целью механизировать или автоматизировать отдельные операции технологического процесса.
Выбор технологической оснастки проводят в соответствии с ГОСТ 14.305-73 путем сравнивания вариантов и определения принадлежности к стандартным системам оснастки. На этом этапе используются отраслевые стандарты ОСТ 4ГО.054.263 – ОСТ 4Г0.054.268.
Оснастка разрабатывается с учетом затрат на реализацию технологического процесса в установленный промежуток времени при заданном качестве изделий. Вид оснастки определяется предварительным выбором используемого оборудования.
При выполнении данного курсового проекта в качестве оснастки был разработан трафарет для нанесения припойной пасты.
Метод трафаретной печати реализуется с помощью металлических или сетчатых трафаретов и металлических шаблонов. Сетчатый трафарет представляет собой жесткую рамку, на которую натянута металлическая или неметаллическая сетка. В отличие от трафаретов, применяемых в технологии гибридных ИМС, трафареты для ПМ имеют большие размеры, что ужесточает требования к допускам на размеры. Необходимо также нанесение большего объема припоя на контактные площадки и так как частицы порошка припоя имеют относительно большие размеры, то это требует применение сеток с более крупными размерами.
При проектировании трафаретов необходимо учитывать минимально допустимый размер окна. Размер окна должен превышать максимальный диаметр припойных шариков в пасте.
На практике минимальные размеры окон определяются, с помощью специальных тестовых трафаретов.
Стандартная толщина трафарета в технологии поверхностного монтажа составляет 200 мкм. Учитывая разнообразие паст, в некоторых случаях могут применяться и другие толщины (например, 175, 150 мкм). Для компонентов с малым шагом выводов (Р 0,4 мм) используются трафареты толщиной 120 мкм чаще всего ступенчатой формы.
Учитывая технологические особенности трафаретной печати и свойства паст, размеры окна (ширина и длина) выбираются меньше размеров контактной площадки. В работе рекомендуются следующие соотношения для расчета размеров окна трафарета [8]:
Wр =W – 0.1мм | (6.1) |
где W – размер контактной площадки (W0,4 мм, толщина трафарета 200 мкм).
Для случая W 0,4 мм (толщина трафарета 120 мкм):
Wр =W – 0.03мм | (6.2) |
При больших размерах окон трафаретов (более 2 мм) в припойной пасте могут появляться пробелы (пустоты, углубления). Для исключения этого недостатка рекомендуется большие окна разделять на несколько малых.
При этом следует использовать следующие рекомендации:
- если размер контактной площадки равен 2 – 3 мм, то число окон выбирается равным 2, если 3 – 4 мм, то 3;
- расстояние между внешней кромкой окна и контактной площадкой составляет 0,05 и 0,015 мм;
- толщина стенок между окнами, исходя из условий механической стабильности трафарета, выбирается от 0,2 до 0,3 мм;
- размер окон должен быть кратен 0,1 мм.
Изначально трафареты изготавливались методом химического травления – для печатных плат, изготовленных по 2-3 классу точности, такие трафареты удовлетворяли техническим условиям.
Однако с появлением на рынке электронных компонентов нового поколения возросли требования к трафаретам для нанесения паяльной пасты.
Решить вопросы возросшей точности и связи с современными пакетами проектирования помогла лазерная резка.
Сфокусированное лазерное излучение, обеспечивая высокую концентрацию энергии, позволяет разрезать практически любые материалы независимо от их теплофизических свойств. При этом можно получить узкие резы с минимальной зоной термического влияния. При лазерной резке отсутствует механическое воздействие на обрабатываемый материал, возникают минимальные деформации, как временные в процессе резки, так и остаточные после полного остывания.
Вследствие этого лазерную резку даже легкодеформируемых и нежестких заготовок и деталей можно осуществлять с высокой степенью точности. Благодаря большой мощности лазерного излучения обеспечивается высокая производительность процесса в сочетании с высоким качеством поверхностей реза. Легкое и сравнительно простое управление лазерным излучением позволяет осуществлять лазерную резку по сложному контуру плоских и объемных деталей и заготовок с высокой степенью автоматизации процесса. Кратко рассмотренные особенности лазерной резки наглядно демонстрируют несомненные преимущества процесса по сравнению с традиционными методами обработки. Поэтому трафарет будем изготавливать методом лазерной гравировки из нержавеющей стали.
На основе информации, полученной в результате конвертации данных из систем проектирования, специальное программное обеспечение рассчитывает координаты движения лазерного луча (а точнее шарика плазмы, создаваемой лазерным лучом в материале), с учетом ширины самого луча, позволяющие ему формировать отверстия различной формы и размеров в листе металла.
Параметры изготовления:
- диаметр луча (ширина реза) – 0,04 мм. Размер получаемой прорези – 0,05 мм, т.к. нужен запас для хода луча. Минимальный размер перемычки в материале между апертурами – не менее 0,1мм;
- точность позиционирования – ±0,001мм;
- максимальный размер рабочего поля – 500х500 мм (полный размер трафарета, с учетом полей до 600 х 600 мм);
- размер отверстия – ±0,005мм;
- конусообразность отверстий по направлению к основанию – ±0,02мм; Конусообразность – это разница между верхним и нижним размерами отверстия.
- максимальная толщина обрабатываемого материала – 0,6мм – до 5кГц;
- частота пульсации луча – до 5кГц (чем выше частота пульсации, тем глаже боковые стенки апертур, что способствует более легкому выскальзыванию паяльной пасты их них).
Трафареты, вырезанные лазером, обладают следующими преимуществами:
- достаточно гладкие стенки и конусообразная форма апертур, что способствует тому, что паяльная паста легко выскальзывает из апертур трафарета при его снятии (подъеме) после выполнения печати;
- высокая геометрическая точность апертур (±0,005мм), позволяющая наносить на контактные площадки платы точно дозированное и повторяемое с каждым разом количество паяльной пасты;
- высокая точность воспроизведения профилей контактных площадок на трафарете, что позволяет легко и надежно совмещать трафарет с печатной платой;
- изготовление трафарета производится непосредственно с данных, полученных с компьютера, что сводит к нулю ошибки вывода фотошаблонов, качества их изготовления, а также качества подготовки поверхности и нанесения фоторезиста на фольгу, как это бывает при изготовлении трафарета методом химического травления;
- нержавеющая сталь, которая служит материалом для таких трафаретов, имеет малую степень растяжения. Поэтому, трафарет не меняет своей формы и рисунок апертур не перекашивается даже после 10 000 циклов печати, что делает трафарет из нержавеющей стали практически вечным в использовании.
Чертеж разработанного трафарета приведен в Приложении.
7 Требования по технике безопасности и охране труда
Технические системы (ТС) – это производственное оборудование, механизмы, машины, аппаратура управления определенной степени сложности, с которыми взаимодействует человек в процессе трудовой деятельности. К ТС в целом, а также к конструкции и ее отдельным частям, рабочим местам, системам управления, средствам защиты, входящим в конструкцию, сигнальным устройствам и конструкциям, обеспечивающим безопасность при монтаже, транспортировке, хранении и ремонте, установлены общие нормативные требования безопасности, приведенные в ГОСТ 12.2.003-91. В требования безопасности обязательно включаются допустимые значения опасных и вредных производственных факторов, которые устанавливаются стандартами подсистемы 1 ССБТ, межотраслевыми и отраслевыми правилами.
Требования по технике безопасности и охране труда должны соответствовать основным требованиям, предъявляемым к сборочным цехам радиотехнических предприятий.
Помещение, должно обладать двумя выходами: основным и запасным, на случай аварии или пожара.
Проходы для персонала не должны быть менее одного метра.
Спроектированный участок, в число оборудования, включает установку пайки, следовательно, необходима организация вытяжной вентиляции, для сведения до минимума вредной, для организма человека, атмосферы.
Организация обеспечения безопасности производственного оборудования (ПО) является составной частью системы управления охраной труда на производстве. Она строится на основе выполнения нормативных требований в процессе приемки вновь поступившего на предприятие ПО, его транспортировки, монтажа, ввода в эксплуатацию и непосредственной эксплуатации, проведение профилактических работ, ремонта и хранения его на предприятии.
Безопасная эксплуатация ПО достигается за счет:
- осуществления систематического контроля за его техническим состоянием;
- своевременного и качественного ремонта оборудования;
- не допуска к работе технически неисправного оборудования.
Отдел главного механика (ОГМ) при этом обязан обеспечивать контроль, исправное состояние, безопасную эксплуатацию в соответствии правилам безопасности (ПБ) технологического оборудования, грузоподъемных и транспортных машин и механизмов. Отдел главного энергетика (ОГЭ) обеспечивает контроль, исправное состояние, безопасную эксплуатацию и соответствие ПБ энергетического и технологического оборудования.
В целях обеспечения безопасности при эксплуатации ПО на предприятиях должен быть организован контроль:
- ежедневный - руководителем участка и общественным инспектором по охране труда профгруппы этого участка;
- еженедельный - руководителем цеха (отдела) и старшим общественным инспектором по охране труда подразделения с привлечением механика, энергетика, технолога, ответственных за исправное состояние и безопасную эксплуатацию оборудования подразделения;
- ежемесячный - комиссиями, возглавляемыми главным инженером, заместителями руководителя и главного инженера предприятия по закрепленным за ними подразделениям;
- плановый - не реже одного раза в квартал - инспекторскими группами и специалистами ОГМ, ОГЭ, санитарной лаборатории предприятия;
- плановый - по плану обследования подразделения - работниками служб охраны труда.
При контроле подлежат осмотру и проверке как ПО, так и его составные части, обеспечивающие безопасные условия труда - заземляющие, оградительные, блокировочные, тормозные и другие специальные технические устройства, знаки безопасности, специальная окраска опасных зон и частей оборудования, оснащенность рабочих мест соответствующими ПБ средствами коллективной и индивидуальной защиты. Выявленные неисправности оборудования, которые могут повлечь за собой аварию или травмирование работающих, должны немедленно устраняться. Включение ПО в работу допустимо только после полного устранения неисправностей.
Безопасность конструкции оборудования должна осуществляться за счет применения:
- технологически обоснованных конструктивных решений и средств, предотвращающих опасные и вредные производственные факторы;
- изоляции токоведущих частей;
- защитного заземления металлических нетоковедущих частей ПО;
- соответствующих средств предупреждения пожаро- и взрывоопасности;
- блокировок для предотвращения ошибочных действий и операций, а также специальных устройств, исключающих самопроизвольное включение;
- ограждения вращающихся частей;
- предупреждающих надписей, знаков, окраски в сигнальные цвета и других средств сигнализации об опасности (предупреждающие надписи и знаки на оборудовании должны иметь четкие очертания, не сливаться с другими надписями).
Оборудование, работа которого связана с нагревом, следует оснащать устройствами и приспособлениями, предотвращающими или резко снижающими выделение в рабочее помещение конвекционного и лучистого тепла. Для обеспечения безотказности работы ПО и качественного исполнения производственного процесса необходимо своевременное техническое обслуживание (смазка необходимых частей установки, проверка изоляции, окраска, регулировка и т.д.).
Для обеспечения безотказности работы ПО и качественного исполнения производственного процесса необходимо своевременное техническое обслуживание (смазка необходимых частей установки, проверка изоляции, окраска, регулировка и т.д.).
Механизмы приводов, движущиеся части оборудования, загрузочные и транспортные устройства, вращающиеся нерабочие части инструмента необходимо закрыть ограждениями, кожухами, экранами и т.п., которые должны быть прочными и не вызывать неудобств при работе и наладке оборудования. Оборудование должно иметь блокирующее устройство, исключающее самопроизвольное включение. Рабочие места, входящие в конструкцию ПО, должны быть безопасными и удобными для работы.
Общие требования к конструкции производственного оборудования:
- применяемые материалы не должны опасное и вредное воздействие на организм человека на всех заданных режимах работы, а также создавать пожаро- и взрывоопасные ситуации;
- сама конструкция оборудования должна исключать на всех режимах работы нагрузки на детали и узлы, способные вызвать разрушения, представляющие опасность для работающих;
- оборудование должно исключить возможность падения, опрокидывания и самопроизвольного смещения при эксплуатации;
- элементы конструкции оборудования не должны иметь острых углов, кромок, заусениц, поверхностей с неровностями, представляющими опасность для рабочих;
- конструкция оборудования, использующего электроэнергию, должна соответствовать требованиям электробезопасности;
- оборудование должно быть пожаро- и взрывобезопасным при эксплуатации, исключать образование источников возгорания, иметь аварийную вентиляцию и систему пожаротушения, в данном случае целесообразно использовать огнетушители марок ОУ-5, ОЧ-8, ЧП-8М, которые применяются для тушения неинтенсивных очагов пожара;
Общие требования к технике безопасности на рабочих местах:
- конструкция рабочих мест, их размеры и взаимное расположение элементов должны обеспечивать безопасность при использовании этого оборудования по назначению;
- размеры рабочих мест и размещение их элементов должны обеспечивать выполнение рабочих операций в удобной позе и не затруднять движения работающего. Руководство ГОСТ 12.2-032-78. При этом конструкция кресла и подставки для ног должны соответствовать эргономическим требованиям и требованиям ГОСТ 12.2.061-81.
Общие требования техники безопасности и экологической безопасности к ТП:
- использование исходных материалов, заготовок, полуфабрикатов, комплектующих изделий и т.п., не оказывающих опасного и вредного влияния на работающих;
- замена ТП и операций, связанных с возникновением опасных и вредных факторов или с их значениями, не превышающими ПДУ, ПДК, ПДВ;
- применение дистанционного управления, комплексной автоматизации при наличии опасных и вредных факторов;
- разработка обеспечивающих безопасность средств управления и контроля ТП;
- применение быстродействующей отсекающей аппаратуры, устройств аварийной защиты;
- использование безотходных технологий замкнутого цикла производства;
- применение сигнальных цветов и знаков безопасности в соответствии с ГОСТ 12.4.086-76, рациональных режимов работы.
Все требования производственной и экологической безопасности излагаются в технологической документации. С ней необходимо ознакомить всех работающих (от ИТР до рабочего), как при обучении, так и при инструктаже в соответствии с ГОСТ 12.1.004-90.
Опасность поражения электрическим током возникает при использовании электрической сети напряжением от 42В. Все доступные для прикосновения токоведущие части оборудования должны быть защищены кожухами. Инструмент для производства электрических работ должен иметь изолирующие ручки из пластмассы или резины. На приборах должны быть указаны: номинальное напряжение питания в вольтах, частота питающего напряжения, потребляемая мощность, ток. Приборы при нормальной эксплуатации не должны нагреваться сверх допустимых значений. Для защиты персонала от напряжения до 1000В и выше применяются ограждения сплошные (кожухи и крышки) и сетчатые. Применяется также блокировка в электроустановках напряжением выше 250В. Должна использоваться сигнализация, привлекающая внимание работающих и предупреждает их неправильное действие. Запрещается ремонт оборудования, находящегося под напряжением. Металлические части приборов класса 01 и I должны быть надежно заземлены.
Создание благоприятных условий труда, исключающих быстрое утомление зрения, возникновение несчастных случаев и способствующих повышению производительности труда, возможно только при правильно спроектированной осветительной системе. Необходимо, чтобы освещенность рабочего места на линии сборки и монтажа составляла около 250 лк. Освещение рабочих мест должно быть комбинированным, когда к общему фоновому освещению добавляется местное, концентрирующее световой поток на рабочее место. Метеорологические условия или микроклимат в производственных условиях определяется следующими параметрами: температура воздуха Т, °С; влажность, %; скорость движения воздуха на рабочем месте u, м/с. Изменение микроклимата приводит к снижению работоспособности человека, поэтому используются оптимальные значения этих параметров для нормальной работы. В радиоэлектронной промышленности большинство работ связано с невысокими физическими нагрузками, поэтому оптимальные значения метеорологических параметров должны быть следующими: Т = 18-21 °С; влажность 40-60 %; u = 0,2-1,0 м/с.
Для устранения загазованности и запыленности воздушной среды производственных помещений должна применяться вентиляция. Основное назначение вентиляции - осуществление воздухообмена, обеспечивающего удаление из рабочего помещения загрязненного воздуха и подачу чистого воздуха. Так как, процесс пайки связан с выделением вредных веществ, необходимо предусмотреть местную вентиляцию для установки пайки волной. Местная вентиляция необходима при покрытии лаком, операции допайки и сушки платы. Необходимо предусмотреть общеобменную и приточную вентиляции для всего помещения. Приточный и удаляемый воздух должен подвергаться обработке (нагреву или охлаждению, увлажнению и очистке от загрязнений).
Для участка цеха, приведенного в приложении Г, необходимо установить вытяжные шкафы 2 Ш-ИЖ в на рабочих местах 1, 4, 6. Для электробезопасности требуется регулярно проверять заземления приборов и установок. Обязательным является соблюдение правил технической эксплуатации электроустановок и правил техники безопасности при эксплуатации электроустановок потребителей. Для обеспечения защиты от случайного прикосновения к токоведущим частям применять:
- изоляцию токоведущих частей;
- изоляцию рабочего места;
- знаки безопасности.
На всех местах цеха необходимо установить местное освещение.
Ко всем зданиям и сооружениям, а также к пожарному инвентарю и оборудованию должен быть обеспечен свободный доступ. Не разрешается загромождать проходы, коридоры, выходы. Легковоспламеняющиеся жидкости, краски, лаки необходимо хранить в плотно закрытых небьющихся емкостях с соответствующими надписями. К работе в цеху допускать лиц, прошедших специальное обучение и инструктаж по технике безопасности.
ЗАКЛЮЧЕНИЕ
В ходе курсового проектирования был разработан технологический процесс сборки и монтажа изделия Система сбора и обработки данных на базе ПК.
Были проведены расчеты технологичности конструкции, доказывающие целесообразность изготовления данного устройства. Были рассмотрены альтернативные варианты маршрутной технологии и выбран более производительный из них. На основании программы выпуска изделия был произведен выбор технологического оборудования, спроектирован участок сборки и монтажа. Промежуточным этапом разработки технологического процесса явилась разработка технологической схемы сборки. Итогом работы стал комплект технологической документации, представленный в Приложении. Разработаны требования по технике безопасности и охране труда. Разработан сборочный чертеж печатного узла, технологическая схема сборки, чертеж оснастки (трафарет для нанесения паяльной пасты).
Список использованных литературных источников
1. Разработка и оформление конструкторской документации РЭА: Справочник / под редакцией Э.Т. Романычевой – М.: Радио и связь, 1989 - 398 с.: ил.
2. Подготовка, контроль и нанесение паяльной пасты [Электронный ресурс]. Режим доступа: http://www.pribor.ru/
3. Каталог оборудования и материалов [Электронный ресурс]. Режим доступа: http://www.dipaul.ru/catalog/SMT/
4. Сборочно – монтажные процессы : учеб. – метод. пособие / В. Л. Ланин [и др.]. – Минск : БГУИР, 2008. – 67 с.
5. Технология радиоэлектронных устройств и автоматизация производства. Курсовое проектирование: Учебное пособие / Ануфриев Л.П., Бондарик В.М. Ланин В.Л., Хмыль А.А. - Мн.: Бестпринт, 2001. – 144 с.: ил.
6. Технология радиоэлектронных устройств и автоматизация проиводства: Учебник / Достанко А.П., Ланин В.Л., Хмыль А.А., Ануфриев Л.П.; Под общей редакцией Достанко А.П.- Мн.: Вышэйшая школа, 2002. – 415 с.: ил.
7. Справочник конструктора-приборостроителя. Проектирование. Основные нормы / В.Л. Соломахо, Р.И. Томилин и др. – Мн.: Выш. Шк., 1988. – 272 с.: ил.
8. Справочник норм расхода материалов ГОСТ 3.118 – 82.
Приложение А Сборочный чертеж
Таблица координат точек
№ точки | Координаты, мм | № точки | Координаты, мм | ||
x | y | x | y | ||
1 | 0 | 0 | 51 | 33,55 | 0 |
2 | 0 | 30 | 52 | 33,55 | 30 |
3 | 40 | 30 | 53 | 34,45 | 30 |
4 | 40 | 0 | 54 | 34,45 | 0 |
5 | 12,1 | 7,2 | 55 | 35,05 | 7,2 |
6 | 12,1 | 8,8 | 56 | 35,05 | 8,8 |
7 | 13 | 8,8 | 57 | 34,45 | 8,8 |
8 | 13 | 7,2 | 58 | 34,45 | 7,2 |
9 | 13,95 | 12,55 | 59 | 35,05 | 12,55 |
10 | 13,95 | 13,45 | 60 | 35,05 | 13,45 |
11 | 14,55 | 13,45 | 61 | 36,1 | 13,45 |
12 | 14,55 | 12,55 | 62 | 36,1 | 12,55 |
13 | 15 | 7,2 | 63 | 37 | 7,2 |
14 | 15 | 8,8 | 64 | 37 | 8,8 |
15 | 15,9 | 8,8 | 65 | 36,1 | 8,8 |
16 | 15,9 | 7,2 | 66 | 36,1 | 7,2 |
17 | 15,45 | 12,55 | 67 | 37 | 12,55 |
18 | 15,45 | 13,45 | 68 | 37 | 13,45 |
19 | 16,05 | 13,45 | 69 | 37,1 | 13,45 |
20 | 16,05 | 12,55 | 70 | 37,1 | 12,55 |
21 | 17,95 | 12,55 | 71 | 38 | 12,55 |
22 | 17,95 | 13,45 | 72 | 38 | 13,45 |
23 | 18,55 | 13,45 | 73 | 39 | 13,45 |
24 | 18,55 | 12,55 | 74 | 39 | 12,55 |
25 | 18,95 | 7,55 | 75 | 39,9 | 7,55 |
26 | 18,95 | 8,45 | 76 | 39,9 | 8,45 |
27 | 19,55 | 8,45 | 77 | 39 | 8,45 |
28 | 19,55 | 7,55 | 78 | 39 | 7,55 |
29 | 19,45 | 12,55 | 79 | 39,9 | 12,55 |
30 | 19,45 | 13,45 | 80 | 39,9 | 13,45 |
31 | 20,05 | 13,45 | 81 | 40 | 13,45 |
32 | 20,05 | 12,55 | 82 | 40 | 12,55 |
33 | 20,45 | 7,55 | 83 | 40,55 | 7,55 |
34 | 20,45 | 8,45 | 84 | 40,55 | 8,45 |
35 | 21,05 | 8,45 | 85 | 44,1 | 8,45 |
36 | 21,05 | 7,55 | 86 | 44,1 | 7,55 |
37 | 23,1 | 12,2 | 87 | 45 | 12,2 |
38 | 23,1 | 13,8 | 88 | 45 | 13,8 |
39 | 24 | 13,8 | 89 | 44,1 | 13,8 |
40 | 24 | 12,2 | 90 | 44,1 | 12,2 |
41 | 26 | 12,2 | 91 | 45 | 12,2 |
42 | 26 | 13,8 | 92 | 45 | 13,8 |
43 | 26,9 | 13,8 | 93 | 44,5 | 13,8 |
44 | 26,9 | 12,2 | 94 | 44,5 | 12,2 |
45 | 32,95 | 26,55 | 95 | 46,1 | 26,55 |
46 | 32,95 | 27,45 | 96 | 46,1 | 27,45 |
47 | 33,55 | 27,45 | 97 | 47 | 27,45 |
48 | 33,55 | 26,55 | 98 | 47 | 26,55 |
49 | 32,95 | 30,55 | 99 | 47,9 | 30,55 |
50 | 32,95 | 31,45 | 100 | 47,9 | 31,45 |
101 | 47 | 21,2 | 121 | 63 | 32,4 |
102 | 47 | 22,8 | 122 | 63 | 33,6 |
103 | 47,9 | 22,8 | 123 | 63,6 | 33,6 |
104 | 47,9 | 21,2 | 124 | 63,6 | 32,4 |
105 | 47,2 | 27,1 | 125 | 65,2 | 28,6 |
106 | 47,2 | 28 | 126 | 65,2 | 29,8 |
107 | 48,8 | 28 | 127 | 65,8 | 29,8 |
108 | 48,8 | 27,1 | 128 | 65,8 | 28,6 |
109 | 47,2 | 30 | 129 | 65,2 | 32,4 |
110 | 47,2 | 30,9 | 130 | 65,2 | 33,6 |
111 | 48,8 | 30,9 | 131 | 65,8 | 33,6 |
112 | 48,8 | 30 | 132 | 65,8 | 32,4 |
113 | 49,9 | 3,25 | 133 | 69,5 | 28,8 |
114 | 49,9 | 6,75 | 134 | 69,5 | 32,25 |
115 | 51,5 | 6,75 | 135 | 71,1 | 32,25 |
116 | 51,5 | 3,25 | 136 | 71,1 | 28,8 |
117 | 63 | 28,6 | 137 | 74,9 | 28,75 |
118 | 63 | 29,8 | 138 | 74,9 | 32,25 |
119 | 63,6 | 29,8 | 139 | 76,5 | 32,25 |
120 | 63,6 | 28,6 | 140 | 76,5 | 28,75 |
Таблица координат точек
№ точки | Координаты, мм | № точки | Координаты, мм | ||
x | y | x | y | ||
1 | 0.000000 | 0.000000 | 51 | 12.310000 | 51.500000 |
2 | 0.000000 | 120.000000 | 52 | 10.310000 | 59.000000 |
3 | 119.950000 | 120.000000 | 53 | 10.310000 | 61.000000 |
4 | 120.050000 | 0.000000 | 54 | 12.310000 | 61.000000 |
5 | 4.050000 | 67.120000 | 55 | 12.310000 | 59.000000 |
6 | 4.050000 | 67.880000 | 56 | 14.050000 | 67.120000 |
7 | 5.950000 | 67.880000 | 57 | 14.050000 | 67.880000 |
8 | 5.950000 | 67.120000 | 58 | 15.950000 | 67.880000 |
9 | 4.050000 | 69.620000 | 59 | 15.950000 | 67.120000 |
10 | 4.050000 | 70.380000 | 60 | 14.050000 | 69.620000 |
11 | 5.950000 | 70.380000 | 61 | 14.050000 | 70.380000 |
12 | 5.950000 | 69.620000 | 62 | 15.950000 | 70.380000 |
13 | 4.050000 | 72.120000 | 63 | 15.950000 | 69.620000 |
14 | 4.050000 | 72.880000 | 64 | 14.050000 | 72.120000 |
15 | 5.950000 | 72.880000 | 65 | 14.050000 | 72.880000 |
16 | 5.950000 | 72.120000 | 66 | 15.950000 | 72.880000 |
17 | 4.050000 | 74.620000 | 67 | 15.950000 | 72.120000 |
18 | 4.050000 | 75.380000 | 68 | 14.050000 | 74.620000 |
19 | 5.950000 | 75.380000 | 69 | 14.050000 | 75.380000 |
20 | 5.950000 | 74.620000 | 70 | 15.950000 | 75.380000 |
21 | 4.050000 | 89.620000 | 71 | 15.950000 | 74.620000 |
22 | 4.050000 | 90.380000 | 72 | 14.050000 | 89.620000 |
23 | 5.950000 | 90.380000 | 73 | 14.050000 | 90.380000 |
24 | 5.950000 | 89.620000 | 74 | 15.950000 | 90.380000 |
25 | 4.050000 | 92.120000 | 75 | 15.950000 | 89.620000 |
26 | 4.050000 | 92.880000 | 76 | 14.050000 | 92.120000 |
27 | 5.950000 | 92.880000 | 77 | 14.050000 | 92.880000 |
28 | 5.950000 | 92.120000 | 78 | 15.950000 | 92.880000 |
29 | 4.050000 | 94.620000 | 79 | 15.950000 | 92.120000 |
30 | 4.050000 | 95.380000 | 80 | 14.050000 | 94.620000 |
31 | 5.950000 | 95.380000 | 81 | 14.050000 | 95.380000 |
32 | 5.950000 | 94.620000 | 82 | 15.950000 | 95.380000 |
33 | 4.050000 | 97.120000 | 83 | 15.950000 | 94.620000 |
34 | 4.050000 | 97.880000 | 84 | 14.050000 | 97.120000 |
35 | 5.950000 | 97.880000 | 85 | 14.050000 | 97.880000 |
36 | 5.950000 | 97.120000 | 86 | 15.950000 | 97.880000 |
37 | 6.500000 | 53.500000 | 87 | 15.950000 | 97.120000 |
38 | 8.500000 | 53.500000 | 88 | 16.305234 | 31.962450 |
39 | 8.500000 | 51.500000 | 89 | 16.305234 | 35.562450 |
40 | 6.500000 | 59.000000 | 90 | 19.505234 | 35.562450 |
41 | 6.500000 | 61.000000 | 91 | 19.505234 | 31.962450 |
42 | 8.500000 | 61.000000 | 92 | 19.200000 | 4.100000 |
43 | 8.500000 | 59.000000 | 93 | 19.200000 | 10.900000 |
44 | 10.705234 | 31.962450 | 94 | 23.000000 | 10.900000 |
45 | 10.705234 | 35.562450 | 95 | 23.000000 | 4.100000 |
46 | 13.905234 | 35.562450 | 96 | 19.200000 | 19.100000 |
47 | 13.905234 | 31.962450 | 97 | 19.200000 | 25.900000 |
48 | 10.310000 | 51.500000 | 98 | 23.000000 | 25.900000 |
49 | 10.310000 | 53.500000 | 99 | 23.000000 | 19.100000 |
50 | 12.310000 | 53.500000 | 100 | 19.000000 | 51.500000 |
101 | 19.000000 | 53.500000 | 151 | 28.450000 | 75.870000 |
102 | 21.000000 | 53.500000 | 152 | 26.550000 | 77.120000 |
103 | 21.000000 | 51.500000 | 153 | 26.550000 | 77.880000 |
104 | 19.000000 | 59.000000 | 154 | 28.450000 | 77.880000 |
105 | 19.000000 | 61.000000 | 155 | 28.450000 | 77.120000 |
106 | 21.000000 | 61.000000 | 156 | 26.550000 | 90.870000 |
107 | 21.000000 | 59.000000 | 157 | 26.550000 | 91.630000 |
108 | 19.000000 | 69.000000 | 158 | 28.450000 | 91.630000 |
109 | 19.000000 | 71.000000 | 159 | 28.450000 | 90.870000 |
110 | 21.000000 | 71.000000 | 160 | 26.550000 | 92.120000 |
111 | 21.000000 | 69.000000 | 161 | 26.588332 | 92.650643 |
112 | 19.000000 | 94.000000 | 162 | 28.450000 | 92.880000 |
113 | 19.000000 | 96.000000 | 163 | 28.450000 | 92.120000 |
114 | 21.000000 | 96.000000 | 164 | 26.550000 | 93.370000 |
115 | 21.000000 | 94.000000 | 165 | 26.550000 | 94.130000 |
116 | 22.810000 | 51.500000 | 166 | 28.450000 | 94.130000 |
117 | 22.810000 | 53.500000 | 167 | 28.450000 | 93.370000 |
118 | 24.810000 | 53.500000 | 168 | 26.550000 | 94.620000 |
119 | 24.810000 | 51.500000 | 169 | 26.550000 | 95.380000 |
120 | 22.810000 | 59.000000 | 170 | 28.450000 | 95.380000 |
121 | 22.810000 | 61.000000 | 171 | 28.450000 | 94.620000 |
122 | 24.810000 | 61.000000 | 172 | 29.000000 | 46.500000 |
123 | 24.810000 | 59.000000 | 173 | 29.000000 | 48.500000 |
124 | 22.810000 | 69.000000 | 174 | 31.000000 | 48.500000 |
125 | 22.810000 | 71.000000 | 175 | 31.000000 | 46.500000 |
126 | 24.810000 | 71.000000 | 176 | 29.000000 | 54.000000 |
127 | 24.810000 | 69.000000 | 177 | 29.000000 | 56.000000 |
128 | 22.810000 | 94.000000 | 178 | 31.000000 | 56.000000 |
129 | 22.810000 | 96.000000 | 179 | 31.000000 | 54.000000 |
130 | 24.810000 | 96.000000 | 180 | 29.000000 | 61.500000 |
131 | 24.810000 | 94.000000 | 181 | 29.000000 | 63.500000 |
132 | 27.000000 | 4.100000 | 182 | 31.000000 | 63.500000 |
133 | 27.000000 | 10.900000 | 183 | 31.000000 | 61.500000 |
134 | 30.800000 | 10.900000 | 184 | 31.550000 | 73.370000 |
135 | 30.800000 | 4.100000 | 185 | 31.550000 | 74.130000 |
136 | 27.000000 | 19.100000 | 186 | 33.450000 | 74.130000 |
137 | 27.000000 | 25.900000 | 187 | 33.450000 | 73.370000 |
138 | 30.800000 | 25.900000 | 188 | 31.550000 | 74.620000 |
139 | 30.800000 | 19.100000 | 189 | 31.550000 | 75.380000 |
140 | 26.550000 | 73.370000 | 190 | 33.450000 | 75.380000 |
141 | 26.550000 | 74.130000 | 191 | 33.450000 | 74.620000 |
142 | 28.450000 | 74.130000 | 192 | 31.550000 | 75.870000 |
143 | 28.450000 | 73.370000 | 193 | 31.524206 | 76.579728 |
144 | 26.550000 | 74.620000 | 194 | 33.450000 | 76.630000 |
145 | 26.550000 | 75.380000 | 195 | 33.450000 | 75.870000 |
146 | 28.450000 | 75.380000 | 196 | 31.550000 | 77.120000 |
147 | 28.450000 | 74.620000 | 197 | 31.550000 | 77.880000 |
148 | 26.550000 | 75.870000 | 198 | 33.450000 | 77.880000 |
149 | 26.550000 | 76.630000 | 199 | 33.450000 | 77.120000 |
150 | 28.450000 | 76.630000 | 200 | 31.550000 | 90.870000 |
201 | 31.550000 | 91.630000 | 251 | 71.900000 | 41.000000 |
202 | 33.450000 | 91.630000 | 252 | 69.300000 | 53.500000 |
203 | 33.450000 | 90.870000 | 253 | 69.300000 | 56.500000 |
204 | 31.550000 | 92.120000 | 254 | 71.900000 | 56.500000 |
205 | 31.550000 | 92.880000 | 255 | 71.900000 | 53.500000 |
206 | 33.450000 | 92.880000 | 256 | 69.300000 | 71.000000 |
207 | 33.450000 | 92.120000 | 257 | 69.300000 | 71.000000 |
208 | 33.450000 | 92.120000 | 258 | 69.300000 | 74.000000 |
209 | 31.550000 | 93.370000 | 259 | 71.900000 | 74.000000 |
210 | 31.550000 | 94.130000 | 260 | 71.900000 | 71.000000 |
211 | 33.450000 | 94.130000 | 261 | 71.550000 | 83.370000 |
212 | 33.450000 | 93.370000 | 262 | 71.550000 | 84.130000 |
213 | 31.550000 | 94.620000 | 263 | 73.450000 | 84.130000 |
214 | 31.550000 | 95.380000 | 264 | 73.450000 | 83.370000 |
215 | 33.450000 | 95.380000 | 265 | 71.550000 | 84.620000 |
216 | 33.450000 | 94.620000 | 266 | 71.550000 | 85.380000 |
217 | 32.810000 | 46.500000 | 267 | 73.450000 | 85.380000 |
218 | 32.810000 | 48.500000 | 268 | 73.450000 | 84.620000 |
219 | 34.810000 | 48.500000 | 269 | 71.550000 | 85.870000 |
220 | 34.810000 | 46.500000 | 270 | 71.550000 | 86.630000 |
221 | 32.810000 | 54.000000 | 271 | 73.450000 | 86.630000 |
222 | 32.810000 | 56.000000 | 272 | 73.450000 | 85.870000 |
223 | 34.810000 | 56.000000 | 273 | 71.550000 | 87.120000 |
224 | 34.810000 | 54.000000 | 274 | 71.550000 | 87.880000 |
225 | 32.810000 | 61.500000 | 275 | 73.450000 | 87.880000 |
226 | 32.810000 | 63.500000 | 276 | 73.450000 | 87.120000 |
227 | 34.810000 | 63.500000 | 277 | 71.550000 | 88.370000 |
228 | 34.810000 | 61.500000 | 278 | 71.550000 | 89.130000 |
229 | 39.300000 | 6.000000 | 279 | 73.450000 | 89.130000 |
230 | 39.300000 | 9.000000 | 280 | 73.450000 | 88.370000 |
231 | 41.900000 | 9.000000 | 281 | 71.550000 | 89.620000 |
232 | 41.900000 | 6.000000 | 282 | 71.550000 | 90.380000 |
233 | 39.200000 | 19.100000 | 283 | 73.450000 | 90.380000 |
234 | 39.200000 | 25.900000 | 284 | 73.450000 | 89.620000 |
235 | 43.000000 | 19.100000 | 285 | 71.550000 | 90.870000 |
236 | 43.100000 | 6.000000 | 286 | 71.550000 | 91.630000 |
237 | 43.100000 | 9.000000 | 287 | 73.450000 | 91.630000 |
238 | 45.700000 | 9.000000 | 288 | 73.450000 | 90.870000 |
239 | 45.700000 | 6.000000 | 289 | 71.550000 | 92.120000 |
240 | 47.000000 | 19.100000 | 290 | 71.550000 | 92.880000 |
241 | 47.000000 | 25.900000 | 291 | 73.450000 | 92.880000 |
242 | 50.800000 | 25.900000 | 292 | 73.450000 | 92.120000 |
243 | 50.800000 | 19.100000 | 293 | 73.100000 | 41.000000 |
244 | 49.619000 | 5.869000 | 294 | 73.100000 | 44.000000 |
245 | 49.619000 | 9.131000 | 295 | 75.700000 | 44.000000 |
246 | 60.000000 | 8.750000 | 296 | 75.700000 | 41.000000 |
247 | 60.381000 | 5.869000 | 297 | 73.100000 | 53.500000 |
248 | 69.300000 | 41.000000 | 298 | 73.100000 | 56.500000 |
249 | 69.300000 | 44.000000 | 299 | 75.700000 | 56.500000 |
250 | 71.900000 | 44.000000 | 300 | 75.700000 | 53.500000 |
301 | 73.100000 | 71.000000 | 351 | 88.200000 | 74.000000 |
302 | 73.100000 | 74.000000 | 352 | 88.200000 | 71.000000 |
303 | 75.700000 | 74.000000 | 353 | 86.800000 | 41.000000 |
304 | 75.700000 | 71.000000 | 354 | 86.800000 | 44.000000 |
305 | 75.600000 | 15.700000 | 355 | 89.400000 | 44.000000 |
306 | 75.600000 | 19.300000 | 356 | 89.400000 | 41.000000 |
307 | 78.800000 | 19.300000 | 357 | 86.800000 | 53.500000 |
308 | 78.800000 | 15.700000 | 358 | 86.800000 | 56.500000 |
309 | 81.200000 | 15.700000 | 359 | 89.400000 | 56.500000 |
310 | 81.200000 | 19.300000 | 360 | 89.400000 | 53.500000 |
311 | 84.400000 | 19.300000 | 361 | 90.259000 | 5.869000 |
312 | 84.400000 | 15.700000 | 362 | 90.259000 | 9.131000 |
313 | 81.800000 | 71.000000 | 363 | 101.021000 | 9.131000 |
314 | 81.800000 | 74.000000 | 364 | 101.021000 | 5.869000 |
315 | 84.400000 | 74.000000 | 365 | 91.800000 | 16.000000 |
316 | 84.400000 | 71.000000 | 366 | 91.800000 | 19.000000 |
317 | 84.050000 | 83.370000 | 367 | 94.400000 | 19.000000 |
318 | 84.050000 | 84.130000 | 368 | 94.400000 | 16.000000 |
319 | 85.950000 | 84.130000 | 369 | 95.600000 | 16.000000 |
320 | 85.950000 | 83.370000 | 370 | 95.600000 | 19.000000 |
321 | 84.050000 | 84.620000 | 371 | 98.200000 | 19.000000 |
322 | 84.050000 | 85.380000 | 372 | 98.200000 | 16.000000 |
323 | 85.950000 | 85.380000 | 373 | 90.600000 | 53.500000 |
324 | 85.950000 | 84.620000 | 374 | 90.600000 | 56.500000 |
325 | 84.050000 | 85.870000 | 375 | 93.200000 | 56.500000 |
326 | 84.050000 | 86.630000 | 376 | 93.200000 | 53.500000 |
327 | 85.950000 | 86.630000 | 377 | 91.500000 | 79.000000 |
328 | 85.950000 | 85.870000 | 378 | 91.500000 | 81.000000 |
329 | 84.050000 | 87.120000 | 379 | 93.500000 | 81.000000 |
330 | 84.050000 | 87.880000 | 380 | 93.500000 | 79.000000 |
331 | 85.950000 | 87.880000 | 381 | 91.500000 | 86.500000 |
332 | 85.950000 | 87.120000 | 382 | 91.500000 | 88.500000 |
333 | 84.050000 | 88.370000 | 383 | 93.500000 | 88.500000 |
334 | 84.050000 | 89.130000 | 384 | 93.500000 | 86.500000 |
335 | 85.950000 | 89.130000 | 385 | 95.600000 | 16.000000 |
336 | 85.950000 | 88.370000 | 386 | 95.600000 | 19.000000 |
337 | 84.050000 | 89.620000 | 387 | 98.200000 | 19.000000 |
338 | 84.050000 | 90.380000 | 388 | 98.200000 | 16.000000 |
339 | 85.950000 | 90.380000 | 389 | 95.310000 | 79.000000 |
340 | 85.950000 | 89.620000 | 390 | 95.310000 | 81.000000 |
341 | 84.050000 | 90.870000 | 391 | 97.310000 | 81.000000 |
342 | 84.050000 | 91.630000 | 392 | 97.310000 | 79.000000 |
343 | 85.950000 | 91.630000 | 393 | 95.310000 | 86.500000 |
344 | 85.950000 | 90.870000 | 394 | 95.310000 | 88.500000 |
345 | 84.050000 | 92.120000 | 395 | 97.310000 | 88.500000 |
346 | 84.050000 | 92.880000 | 396 | 97.310000 | 86.500000 |
347 | 85.950000 | 92.880000 | |||
348 | 85.950000 | 92.120000 | |||
349 | 85.600000 | 71.000000 | |||
350 | 85.600000 | 74.000000 |
Схема сборки
Приложение Б Технологическая документация
Ведомость материалов
Ведомость оснастки
Приложение В План участка цеха
Маршрутные карты
УТВЕРЖДАЮ | Сержанин П.Н. |
Грозберг Ю.Г. | |||
Система сбора и обработки данных на базе ПК |
|||||
СПН.446126.013 | |||||
КОМПЛЕКТ ДОКУМЕНТОВ | на технологический процесс сборки и монтажа | Системы сбора и обработки данных | На базе ПК |
||
ПГУ Т.08.01 | |||||
СОГЛАСОВАНО | Разработал | Проверил | Т. контроль | Н. контроль | Утв. |
Спецификация
Форма |
Зона | Поз | Обозначение | Наименование | Кол | Прим. |
10 | 1210 0,1мк | 1 | C9 | |||
11 | 1210 0,1мк | 1 | C 10 | |||
12 | 1210 0,1мк | 1 | C 11 | |||
13 | 1210 0,1мк | 1 | C 12 | |||
1 4 | 1210 0,1мк | 1 | C 13 | |||
Микросхемы | ||||||
15 | MAX4541CPA | 1 | DA1 | |||
16 | КР1157ЕН1 | 1 | DA 2 | |||
17 | КР1446УД1А | 1 | DA 3 | |||
18 | MAX4541CPA | 1 | DA 4 | |||
19 | REF02BP | 1 | DA 5 | |||
20 | MAX202CPE | 1 | DA 6 | |||
21 | AT90S4433 – BP1 | 1 | DD1 | |||
Дроссели | ||||||
22 | 10 мкГ ± 10% BI Technologies | 1 | L1 | |||
Резисторы | ||||||
2 3 | Р1-12M-0,125-510 Ом ±10% | 1 | R1 | |||
2 4 | Р1-12M-0,125-510 Ом ±10% | 1 | R2 | |||
2 5 | Р1-12M-0,125-240 Ом ±10% | 1 | R3 | |||
2 6 | Р1-12M-0,125-620 Ом ±10% | 1 | R4 | |||
2 7 | Р1-12M-0,125-100 Ом ±10% | 1 | R5 | |||
2 8 | Р1-12M-0,125-7,5 кОм ±10% | 1 | R6 |
Форм. |
Зона | Поз. | Обозначение | Наименование | Кол. | Прим. |
2 9 | Р1-12M-0,125-6,2kОм ±10% | 1 | R 7 | |||
30 | Р1-12M-0,125-30kОм ±10% | 1 | R 8 | |||
31 | Р1-12M-0,125-30kОм ±10% | 1 | R 9 | |||
32 | Р1-12M-0,125-330 Ом ±10% | 1 | R 10 | |||
33 | Р1-12M-0,125-330 Ом ±10% | 1 | R 11 | |||
Диоды | ||||||
34 | АЛ307БМ | 1 | VD1 | |||
35 | АЛ307БМ | 1 | VD 2 | |||
Разъёмы | ||||||
36 | PLD – 2 | 1 | XP1 | |||
37 | DBR9-F | 1 | XS1 | |||
Кварцевый резонатор | ||||||
38 | HC-49SM | 1 | ZQ1 |
Приложение Г Чертеж оснастки
Эскизные карты