Технология автоматизации литейных процессов
СОДЕРЖАНИЕ: 2. Введение. В настоящее время 70 % машиностроительного комплекса, предприятий нефтеперерабатывающей, газовой, судостроительной, автомобильной промышленности, предприятий министерства путей сообщения имеют собственные литейные производства.1.
2. Введение.
В настоящее время 70 % машиностроительного комплекса, предприятий нефтеперерабатывающей, газовой, судостроительной, автомобильной промышленности, предприятий министерства путей сообщения имеют собственные литейные производства.
На предприятиях специализирующихся на выпуске продукции для нефтегазовой и автомобильной промышленности, таких как ОАО «Пензатяжпромарматура», г. Пенза, ОАО «Тяжпромарматура» г. Алексин, ОАО «Юго-Камский машзавод им. Лепсе», ОАО «КАМАЗ-Металлургия», ООО «ЭНЕРГОМАШ (Белгород)»
Открытое акционерное общество КАМАЗ - Металлургия является крупнейшим производителем литья в РФ. В таблице 4 представлены общие сведения о предприятии, объемы производства литья за 2003, 2004 годы соответственно.
Показатели |
2003 год |
2004 год |
Объемы реализации продукции на внутренний рынок*, тыс. руб. |
998 138 |
1 365 641 |
Объемы реализации продукции на экспорт, тыс. руб. |
204 662 |
181 485 |
Всего *, тыс. руб. |
1 202 800 |
1 547 126 |
Литейный завод *, тыс. руб. |
859 055 |
1 178 383 |
Литейный завод производит отливки, как из чугуна, так и из стали. Рассмотрим технологические возможности предприятия.
Чугунное литье. Общая площадь корпуса 172800 кв.м., производственная мощность - 222,72 тыс. тонн отливок в год, включая: серый чугун, высокопрочный чугун. Производство представляет законченный технологический цикл массового производства отливок.
Плавка металла ведется дуплекс - процессом в печах Swindell - Dressler. Производство оснащено девятью печами плавки емкостью 50 тонн и семью печами выдержки емкостью 75 тонн.
Транспортировка жидкого металла производится с использованием транспортной системы Cleveland Crane, заливка - заливочными установками Georg Fisher и Seaton.
Формовочный цех оснащен пятью автоматическими формовочными линиями CE-Cast и тремя линиями Disamatic. Формовочное оборудование позволяет изготавливать отливки любой сложности с высокой степенью точности.
Стержни изготавливаются с использованием процесса Hot-Box и Cold-Box с продувкой SO2 на 67-ми стержневых машинах Sutter.
Завершен монтаж одной из двух закупленных предприятием автоматических формовочных линий фирмы HWS с размерами опок 1500х1100х400/400мм, на очереди линия с размерами опок 1100х750х300/300мм.
Экспресс - анализ и анализ качества отливок ведется с использованием современных методов и средств контроля на спектрометрах фирм Baird, Perkin-Elmer, Spectro и ARL.
Термообработка, очистка и обрубка отливок ведется на оборудовании фирм Holcroft, Pangborn и Cross-Freser.
Данные линии позволят обеспечить главное условие конкурентоспособности, возможность получения сложных тонкостенных отливок высокой точности, применяемых в машиностроении.
Стальное литье. Общая площадь корпуса 49300 кв.м. Производственная мощность - 56,85 тыс. тонн отливок из углеродистых и жаропрочных сталей в год, в том числе 4,42 тыс. тонн точных стальных отливок по выплавляемым моделям.
Производство оснащено девятью электрическими дуговыми печами ДСП-12Н2 емкостью 12 тонн и тремя печами ИСТ 1/05. Имеются две автоматические формовочные линии CE-Cast и одна линия Disamatic. Стержни изготавливаются с использованием процесса Shalco на машинах U900 и 315E этой фирмы. Термообработка, очистка и обрубка отливок осуществляется на оборудовании Pangborn и Holcroft.
ОООЭнергомаш (Белгород), также осуществляет производство стального литья. Данные об объемах литья отсутствуют.
Группа компаний ЭНГЕРГОМАШ - крупнейшая группа компаний энергетического машиностроения России - является одним из лидеров отечественного машиностроения. Технологические возможности ООО Энергомаш (Белгород) позволяют осуществлять производство стального фасонного литья и поковок из углеродистых и среднелегированных сталей. С 1963 года имеется богатый опыт в изготовлении отливок для общего машиностроения, в том числе арматурного литья.
Продукция и услуги: стальные отливки для общего машиностроения развесом от 50 до 3500 кг, из углеродистых и среднелегированных сталей. Поковки брусков, валов, фланцы воротниковые, раскатные кольца из сталей 09Г2С, 10Г2, 12Х1МФ, 15Х1М1Ф, 15ГС, СТ.20, 40ХН2МА, 5ХНМ.
На сегодняшний день литье данного предприятия имеет высокое качество стального литья и приемлемые цены.
Литейное производство ОАО «Икар», активно присутствует на рынке производства и реализации литья с 1961 года, основной номенклатурой литейного цеха была чугунная арматура и производство литья для Норильского металлургического комбината.
В 1994 в состав литейного производства были введены мощности еще одного цеха – производитель стального литья проходов Ду50 – Ду100. С этого момента роль литейного производства ОАО «Икар» возросла, так как она стала обеспечивать внутреннюю потребность производства ОАО «Икар» и рынка потребления в стальной арматуры малых проходов.
Важнейшим фактором, обеспечивающим устойчивые позиции на рынке для ОАО «Икар», является приобретение и запуск комплекса фирмы АВВ в 1997 г., с введение этих мощностей литейное производство ОАО «Икар» расширило спектр номенклатуры производства стальнойодство литья для Магнитеских свойств допускаюстся отклонениятветствовать нормам приведенным в арматуры до Ду 500 и давлением до 250 кгс/см2 что позволило устойчиво находится на рынке производства арматуры. В условиях изменяющегося рынка производство арматуры в период с 2003 до 2004 г. имело не высокую рентабельность и даже «выигранные тендеры на производство арматуры» для нефтегазоперерабатывающего комплекса не сулили больших прибылей. Причиной низкой рентабельности продукции ОАО «Икар» являлось высокая себестоимость литых заготовок. Мероприятия, направленные на снижение материалоемкости, снижение трудозатрат не принесли ощутимых результатов. Вопрос стал ясен, без увеличения, объемов выпуска стального литья значительного снижения себестоимости не добиться и соответственно в условиях сегодняшнего рынка производства арматуры удержать позиции будет не легко.
И в 2004 г. решением совета директоров в составе ОАО «Икар» было выделено, предприятие получившее название СЧЛЗ (сталечугунолитейный завод) работающее на условиях неполного хозяйственного расчета, которое выделило сбытовые и маркетинговые направления, ценообразование и учет на предприятии.
На сегодняшний день литейное производство (СЧЛЗ) является необъемлемой частью ОАО «Икар», составляя его основу. Общий объем выпуска товарной продукции завода в месяц составляет около 27,0 млн. руб., в том числе на сторону 5 млн.рублей, и около 324 млн. руб. в год.
Диаграмма 1. Объем производства литья в и 2004 – 2006 г.г.тонн (по данным СЧЛЗ ОАО «Икар»).
Диаграмма 2. Объем производства товарной продукции и 2004 – 2006 г.г., тыс. руб с НДС (по данным СЧЛЗ ОАО «Икар»).
В сегодняшних условиях динамично растущего рынка потребления литейных заготовок со специальными свойствами, с высокими требованиями по качеству необходимо постоянно улучшать технологические процессы.
Проводить техническое перевооружение литейных цехов, внедрять современное оборудование мировых производителей, таких как HWS
(HEINRICH WAGNER SINTO ) формовочные машины проходного типа
|
высокопроизводительное оборудо-
вание позволяющее получать формы
высокого качества с необходимыми
физическими свойствами. Данное
оборудование позволяет экономить
материалы за счет применения реге-
рации отработанной смеси.
Общая часть
1. Характеристика материала.
Для выполнения курсового проекта выбрана деталь корпус задвижки с проходом 150 мм и давлением 63 кгс/см 2. Данная деталь корпус используется для оборудования нефтяной промышленности. Деталь корпус служит для совмещения трубопроводов между собой и других деталей корпусов меньшего прохода, в транспортных системах на скважинах нефтяных месторождений. Для данной детали корпуса для изготовления выбран материал сталь 30ХМЛ. Сталь 30ХМЛ относится к группе хладостойких материалов. В стали 30ХМЛ присутствуют элементы хрома и молибдена они способствуют повышению ударной вязкости и улучшению хладостойких свойств. Кроме этого низкое содержание вредных элементов, таких как сера и фосфор способствует улучшению механических свойств.
Аналоговыми деталями корпуса могут быть детали используемых в устройствах нефтетранспорта и нефтеперекачки больших проходов. Подобные детали испытывают высокое давление от 63 до 160 кгс/м2 .
С |
Si |
Mn |
Cr |
Mo |
Ni |
S |
P |
0,22 -0,35 |
0,2 - 0,5 |
0,5 - 0,9 |
0,8 - 1,2 |
0,2 - 0,35 |
не более 0,15 |
не более 0,04 |
не более 0,04 |
Химический состав стали 30ХМЛ ГОСТ977-88.
Таблица № 1
Механические свойства стали.
Таблица № 2
в |
0.2 |
КСV - 60 |
||
550 |
370 |
15 |
50 |
250 |
2. Технические условия.
Деталь переходник изготавливается из заготовки – отливки полученной
методом литья в землю:
1. Точность отливки 12-0-0-12 по ГОСТ26645-89.
2. Неуказанные литейные радиусы 5 мм.
3. Не указанные формовочные уклоны 2 в сторону увеличения тела отливки.
4. Требования к отливке по СТ ЦКБА 014-2004
5. Допускается замена стали 30ХМЛ ГОСТ 977-88 на сталь ХМ25Л ТУ4112-017-00218147-99 отливка 3 группы в 441, 0.2 235, 19, КСV – 60 400.
6. Допускается для исполнений КЗ13008 -150А.1 заменитель материала на сталь 25Л ГОСТ 977-88 отливка 3 группы в 441, 0.2 235, 19, КСV – 40 300.
7. Маркировать по ГОСТ 4666-75 технические данные, товарный знак марку материалов. Допускается маркировать ударным способом. Шрифт 10-Пр3 ГОСТ26.008-85. Место под маркировку зачистить Rа 50.
8. Маркировать номер плавки. Допускается маркировать ударным способом. Шрифт 10-Пр3 ГОСТ26.008-85. Место под маркировку зачистить Rа 50.
9. Допускаются остатки питателей до 3 мм.
10. Допускаются остатки прибылей до 5 мм.
Отливка корпус КЗ13008-150А.1 изготовленная из стали 30ХМЛ подвергается техническому контролю размеров указанных в чертеже отливки. Проверки химического состава. Так как отливка корпус относится к III группе по ГОСТ 977-88. Кроме химического состава стали определяют механические свойства плавки, из которой из отлита данная отливка. Испытания на прочность образцов плавки проводят в специально металлографической лаборатории предприятия. Испытания на специальных стендах высокого давления на прочность номинальным давлением 63 ккс/м2 водной средой и полуторным давлением воздухом.
Определение ударной вязкости при диапазоне температур – 60 – 450 методом Шарпи по ГОСТ9454-78
Технологическая часть
1.Анализ технологичности конструкции детали.
Отливка корпус КЗ13008-150А.1 представляет собой конструкцию имеющую в основе совокупность взаимно пересекающихся цилиндрических тел вращения. Рис № 1.
Рис № 1
Соединенные тела вращения имеют плавные радиуса
перехода R от 5 до 30 мм. Отливка корпуса не является техноло-
гичной так как он имеет наличие тепловых узлов и неравномерных утолщений в своей конструкции. Рис № 2
![]() |
Рис № 2
Максимальная толщина стенок отливки 51 мм и минимальная толщина 18 мм. Приведенная толщина составляет 34 мм. В дальнейшем при расчете литниковой системы отливки мы будем использовать значение приведенной толщины стенки отливки корпуса КЗ13008-150А.1.
Отливка корпуса имеет обрабатываемые поверхности А; Б по обработке магистральных фланцев, С по обработке центрального фланца и Д обработка по седла.
2. Определение припусков на обработку.
При определении припусков на механическую обработку мы используем справочные данные ГОСТ 26645-85 (Допуски размеров, массы и припуски на механическую обработку для отливок из металлов и сплавов).
Порядок определения припусков на механическую обработку заключается в определения способа производства, класса точности отливки, допуски поверхностей. В технических требованиях отливки корпуса КЗ13008-150А.1 указано – точность отливки 12-0-0-12. Первая цифра указывает на точность отливки 12 класса размерной точности, вторая цифра степень коробления в
нашем случае не определена, третья цифра степень точности поверхностей в нашем случае не определена, четвертая цифра 12 класса точности масс.
По таблице № 9 ГОСТ26645-85 определяется размерная точность отливки в зависимости от способа производства, материала и массы отливки. Отливка корпус, изготавливается методом литья в землю имеет массу 93 кг. При массе до 100 кг материале сталь и использования при формообразовании песчано-глинистую форму с влажностью до 2,5 % и прочностью более 100 кПа Размерная точность соответствует 7 – 12 классу. Так как в нашем случае степень коробления и степень точности поверхностей не определена, то назначение припусков на механическую обработку определяем по классу размерной точности . По таблице № 1 ГОСТ26645 -85 для 12 класса размерной точности определяем для каждого размера (имеющего назначенную обработку) отливки допуски в диаметральном выражении.
Припуски на обработку (на сторону) назначают на каждую обрабатываемую поверхность отливки.(Рис № 2) Минимальный литейный припуск назначаем в соответствии с таблицей № 5. Общий припуск на механическую обработку назначают в соответствии с таблицей № 6.
Для обработки магистральных фланцев корпуса при размере 435 мм допуск на размер составит 10 мм 5 мм на сторону. По таблице № 5 минимальный литейный припуск для 12 класса составляет 2,5 мм. По таблице № 6 общий припуск на допуск 5 мм составит 9 мм в диаметральном выражении на сторну 4,5 мм. Припуск на размер 435 мм составит 7 мм. На сторону. Остальные припуски определяем тем же путем. (табл № 3)
Таблица № 3
Размер |
Допуск на размер на сторону |
Минимальный литейный припуск |
Общий припуск |
Припуск на размер на сторону |
435 |
5,0 |
2,5 |
4,5 |
7,0 |
226 |
4,0 |
2,5 |
4,25 |
6,75 (7) |
44 |
2,5 |
2,5 |
2,55 |
5,05 (5) |
164 |
3,5 |
2,5 |
3,05 |
5,55 (6) |
3. Анализ существующего технологического процесса. Выбор метода производства отливки.
Отливка корпуса КЗ13008-150А.1 изготовляется в литейном цехе сталечугуннолитейного завода ОАО « Икар» Завода трубопроводной арматуры.
Вид шихты |
Марка |
Стальной лом |
1А – 2А |
Ферросилиций |
ФС- 45 |
Феррохром |
ФХ-001А |
Марганец металлический |
Мр995 |
Ферромолибден |
ФМо60 |
Возврат производства |
30ХМЛ |
В качестве основных материалов используется покупная шихта табл № 4:
Таблица № 4
Шихта поступает от надежных поставщиков с наличием сопроводительных документов, сертификатов качества.
Расплав шихты ведется в индукционной печи производства Германско-Американской фирмы АБР (Asea Braun Pilar). Печь IFM-3/4,0 имеет емкость 4 тонны производительность 2 тонны в час. Печь среднечастотная 450 Гц мощность 2 МВт. Управляемая, процессором фирмы «Simens» с помощью управляемой программы Prodapt. В качестве загрузочных устройств используются загрузочные бадьи и контейнеры. Контроль химического состава осуществляется двумя способами, экспресс-анализ спектральной установкой ДФС-51(спектрометром) и химическим способом с помощью различных реактивов.
Разливка металла проводится чайниковыми ковшами емкостью 1; 2 тонн. Ковши футерованы в соответствии с правилами промышленной безопасности ПБ-11-551-03. Двухрядной футеровкой из шамотного кирпича с применением в качестве связующего глину марки НУ-2. Сушка ковшей осуществляется на специальных стендах, работающих на природном газе. Температура сушки 600 – 800 С время сушки определено опытным путем, составлены графики сушки для каждого типоразмера ковша.
В качестве формовочных материалов применяются:
Таблица № 5
Вид шихты |
Марка |
|
1. |
Песок кварцевый |
3К3О203 |
2. |
Глина формовочная |
НУ-2 |
3. |
Порошок из глины молотой |
ПГМС23 |
4. |
Керосин для технических целей |
КТ-1 |
5. |
Литапарм для модельной оснастки |
|
6. |
Двуокись углерода газообразная |
|
7. |
Натр едкий технический |
ТР |
8. |
Силикат натрия раств.мод.2,6-3,0 |
|
9. |
Уголь гранулированный |
ГБ |
10. |
Стеклоткань |
КС 11-ЛАП-2 |
11. |
Мазут |
Смесеприготовление формовочной смеси ОФ и облицовочной смеси СХТ проводится в смешивающих бегунах мод 15101 с вертикально-вращающимся катками. В состав смеси ОФ (наполнительная смесь) входит песок, эмульсия на основе глины НУ-2, мазут, вода. В состав облицовочной смеси СХТ входит жидкое стекло, приготовленное на основе силиката натрия растворимого и едкого натра.
Изготовления форм ведется на формовочных машинах встряхивающего типа, вибрационных столах. Типы формовочных агрегатов мод 22506; мод 22505; мод 703М. вибрационные столы собственного изготовления.
Изготовление стержней ведётся по двум технологиям, из смесей на основе жидкого стекла и химически твердеющих смесей. Стержни, изготавливаемые из жидко-стекольных смесей, изготавливаются вручную. Стержни из химически твердеющих смесей изготавливают с помощью смесителя непрерывного действия мод. 4727 производства Санкт-Петербург.
В качестве выбивного оборудования применяются выбивные решетки вибрационного типа.
Для выполнения финишных операций применяется очистное оборудование, дробеметные камеры, 42832, дробеметные барабаны 42223, 42216. голтовочные барабаны. Обрезку литниковых систем выполняют газовой резкой смесью кислорода и природного газа. Обрубку отливок проводят специальным, пневмо-инструментом и ручными средствами удаления заливов и пригара, молотки, зубила.
Отливка корпуса КЗ13008-150А.1 изготавливается по вышеуказанной технологии базовый вариант изготовления в формах со смесью ОФ и облицовкой СХТ. Стержни изготовлены из смеси ХТС.
При технологической разработки для получения качественной заготовки использована расчетная литниковая система, с применением отводных прибылей атмосферного давления на магистральных и центральном фланцев. Кроме этого прибыль установлена в центре для питания мест уплотнения корпуса. Рис № 3.
Рис № 3
Вес залитой формы составляет 240 кг. при весе отливки 93 кг выход годного составит: (93 / 240) х 100 = 38,75 %.
Потребное количество жидкого металла для изготовления тонны литья определяется в зависимости от процента выхода годного от металлозавалки
= 2580,0
где Мз – металлозавалка;
ВГ – вес годного литья в т (1000 кг);
Кгод – % выхода годного литья
Количество жидкого металла будет получено за вычетом потерь в связи с угаром шихты, составляющим примерно 5-6%
= 2734,0
где Куч – % угара
Отходы на литники (возврат собственного производства) определяются как разница между величиной жидкого металла и годного литья. Q воз = (100 –Кгод + Куч ) х Мз / 100 = (100 -38,75 +6) х2580,0))/100 = 1755,0
Целью любого проекта является получение экономического эффекта от внедрения, какого либо новшества. Необходимо предложить на обсуждение техническое решение, которое позволит получать прибыль с наименьшими затратами или затраты не будут существенно влиять на получение качественного продукта.
В своей работе предлагаем применить в технологии, на сегодня широко применяемые за рубежом, специальные вставки. Вставки служат для формирования в форме «прибылей». Кроме этого вставки имеют свойство уменьшать теплоотдачу от отливки к форме, тем самым создавать условие для направленной кристаллизации и питания тепловых узлов отливки. Для определения их параметров необходимо правильно рассчитать элементы литниковой системы.
4. Расчет параметров литниково-питающей системы
Расчет литниковой системы производят применительно к условиям заливки форм: или из поворотного чайникового ковша, что практикуется при изготовлении мелких отливок, или стопорного ковша
В первом случае строят запертые литниковые системы с отношением Fпит : Fл.ход : Fст = 1,0 : 1.05 : 1.15 ( 1,0 : 1.3 : 1.6) где л.ход –общее сечение литниковых ходов после стояка.
При изготовлении крупных отливок, когда литниковая система собирается из керамических элементов соотношение: Fпит : Fпит : Fл.ход = 1 : 1 : 1 или ее делают расширяющей.
Определение оптимальной продолжительности заливки производят по формуле:
= S1
= 1,4 х
= 28,19 сек.
Где:
- оптимальная продолжительность заливки;
S1 – коэффициент времени, установленный по таблице;
- преобладающая или средняя толщина стенки отливки в мм;
G – Вес одной отливки плюс вес литников и прибылей приходящихся на одну отливку в кг.
Значения коэффициента 1
для стальных отливок.
Температура и жидкотекучесть метплла |
Подвод металла |
||
Снизу сифоном в толстостенные части отливки |
На половине высоты или ступечатый (комбинированый) |
Сверху равномерно в тонкостенные части отливки. |
|
Нормальные |
1,3 |
1,4 |
1,5 – 1,6 |
Повышенные |
1,4 – 1,5 |
1,5 – 1,6 |
1,6 – 1,8 |
Таблица № 6
Определение площади сечения питателей производят по формуле.
Fпит
=
Hср
=
х
350 = 5,87 см2
.
Где Hср - средний расчетный напор
- общий коэффициент расхода в литниковой системе;
Значение коэффициента стальных отливок
Таблица № 7
Характер отливки |
Сопротивление формы |
||
Большое |
Среднее |
Малое |
|
В сырую |
0,25 |
0,32 |
0,42 |
В сухую |
0,3 |
0,38 |
0,5 |
Определение площади сечения литникового хода и стояка производится из отношения Fпит : Fпит : Fст = 1,0 : 1,2 : 1,4 или 1,0 : 1,15 : 1,3
Уклон стояка делается из расчета 1 мм на 100 мм высоты.
Мы выбираем соотношения Fпит : Fшл : Fст = 1,0 : 1,2 : 1,3 так как, имеется 2 питателя, соотношения в см2 5,87 : (5,87 х 1,2) х 2 = 14,09 : (14,09 х 1,3) х 2 = 36,65.
Таким образом, литниковая система выглядит в соотношении:
5,87 : 14,09 : 36,65
![]() |
Питатель: 5,87 = 2,8 х 2,1
28
![]() |
21
Шлаковик: 14,09 = 3,36 х 2,52
33,6 (34)
25,2 (26) 68,4 (70)
![]() |
Стояк: 36,65 = 3,14 х 3,42 2
Для выбора размеров изоляционных вставок необходимо определить условный диаметр прибыли. При определении условного диаметра прибыли необходимо вычислить площадь поперечного сечения и периметр того места которое необходимо питать.
Рис № 4
F = 9,8 х 4,4 = 43,12 см2 Р = (9,8 + 4,4) х 2 = 28.4 см
Dусл = (4 х F / Р) х К вст = (4 х 43,12 / 28,4) х 1,2 = 7,89 см =78,9мм
Где К вст - поправочный коэффициент для изоляционной вставки. От 1,2 – 1,5
Из ряда используемых в производствах и размещенных на сайте «огнеупорные материалы» из изоляционных вставок ближайшая по диаметру d = 75 мм. Все остальные размеры вставки есть в таблицах вышеуказанного сайта.
Конструкция полной литниковой системы будет выглядеть:
Предлагаемый вариант литниково-питающей системы.
Рис № 5
Вес залитой формы составляет 205 кг. при весе отливки 93 кг выход годного составит: (93 / 205) х 100 = 45,36 %. Рис № 5.
Потребное количество жидкого металла для изготовления тонны литья определяется в зависимости от процента выхода годного от металлозавалки
= 2204,0
где Мз – металлозавалка;
ВГ – вес годного литья в т (1000 кг);
Кгод – % выхода годного литья
Количество жидкого металла будет получено за вычетом потерь в связи с угаром шихты, составляющим примерно 5-6%
= 2336,0
где Куч – % угара
Отходы на литники (возврат собственного производства) определяются как разница между величиной жидкого металла и годного литья. Q воз = (100 –Кгод + Куч ) х Мз / 100 = (100 -45,36 +6) х2204,0))/100 = 1336,0
Существующую рассчитанную литниковую систему необходимо проверить на эффективность с помощью программы моделирования Solid Cast.
Модель для проверки расчетов литниковой системы:
|
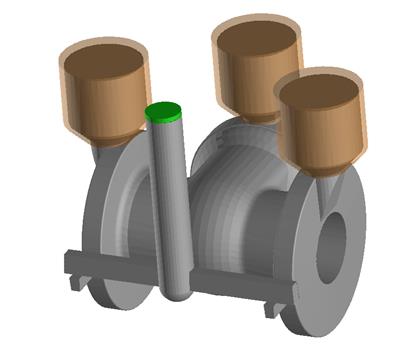
|
Как видно из результатов моделирования отливка достаточно плотная, при более детальной проверки видно как происходит кристаллизация отливки.
Рис № 8
Разрез с боку
|
Рис № 9
5. Расчет шихты для получения заданной марки материала.
Расчет шихты для получения заданного химического состава.
Расчет шихты для стали 30ХМЛ ГОСТ проводится по формулам. M мат =
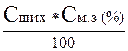


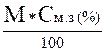
Таблица № 8
Наименование и марка |
C |
Si |
Mn |
S |
P |
|||||||
сод.ших |
сод.ж.мет |
сод.ших |
сод.ж.мет |
сод.ших |
сод.ж.мет |
сод.ших |
сод.ж.мет |
сод.ших |
сод.ж.мет |
% |
кг |
|
Лом стальной 1А |
ших |
M мат |
C ших |
M мат |
C ших |
M мат |
C ших |
M мат |
C ших |
M мат |
С м.з |
|
Фланец. |
C ших |
M мат |
C ших |
M мат |
C ших |
M мат |
C ших |
M мат |
C ших |
M мат |
С м.з |
М м.з |
Чугун передельный |
C ших |
M мат |
C ших |
M мат |
C ших |
M мат |
C ших |
M мат |
C ших |
M мат |
С м.з |
М м.з |
Ферромарганец |
C ших |
M мат |
C ших |
M мат |
C ших |
M мат |
C ших |
M мат |
C ших |
M мат |
С м.з |
М м.з |
Сумма |
M мат |
M мат |
M мат |
M мат |
M мат |
|||||||
Угар в % |
К |
К |
К |
К |
К |
М |
||||||
С учетом угара |
M мат |
M мат |
M мат |
M мат |
M мат |
Химический состав стали 30ХМЛ ГОСТ977-88.
Таблица № 9
С |
Si |
Mn |
Cr |
Mo |
Ni |
S |
P |
0,22 -0,35 |
0,2 - 0,5 |
0,5 - 0,9 |
0,8 - 1,2 |
0,2 - 0,35 |
не более 0,15 |
не более 0,04 |
не более 0,04 |
В состав шихты войдут материалы, при металлозавалке 2236 кг возврат составит 1336 кг или
Таблица № 10
Вид шихты |
Марка |
% |
|
1 |
Стальной лом |
1А – 2А |
39.4 |
2 |
Ферросилиций |
ФС- 45 |
0.2 |
3 |
Феррохром |
ФХ-001А |
0.2 |
4 |
Марганец металлический |
Мр995 |
0.2 |
5 |
Ферромолибден |
ФМо60 |
0,25 |
6 |
Возврат производства |
30ХМЛ |
59,74 |
7 |
Никель |
Н1 |
0.01 |
100% |
Расчет ведем по каждому виду шихты и элементу.
Стальной лом :
M мат =
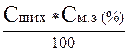

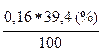
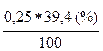

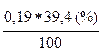
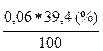
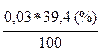
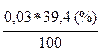

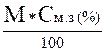
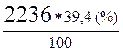
Возврат стали 30ХМЛ :
M мат =
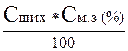

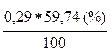
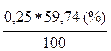
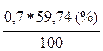
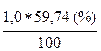
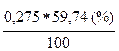
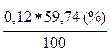
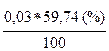
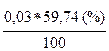

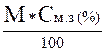
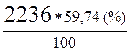
Ферросилиций :
M мат =
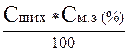







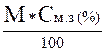
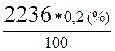
Феррохром :
M мат =
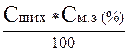







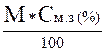
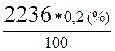
Марганец металлический :
M мат =
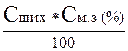




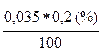


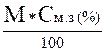
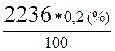
Ферромолибден :
M мат =
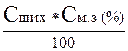

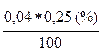
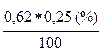
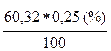
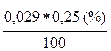
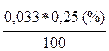

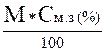
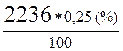
Никель :
M мат =
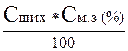

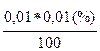
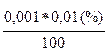
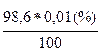

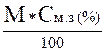
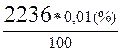
Суммируем все полученные результаты по каждому элементу и умножаем на Kуг :
С
= М Kуг
= (0,063 + 0,1702 + 0,0004 + 0,00004 + 0,00004 + 0,000098 + 0,0001 + 0,000001 ) * 0,98 = 0,2297
Si
= М Kуг
= (0,0985 + 0,1493 + 0,0004 + 0,00004 + 0,00017 + 0,0015 + 0,0000001 ) * 1,05 = 0,3576
Mn
= М Kуг
= (0,6304 + 0,418 + 0,002 + 0,1972) * 0,6 = 0,7488
Cr = 0,07486 + 0,5974 + 0,146 = 0,8183
Mo = 0,1642 + 0,166 + 0,1508 = 0,3151
Ni = 0,0236 + 0,0716 + 0,0098 = 0,1052
S = 0,0118 + 0,0179 + 0,00004 + 0,000012 + 0,00007 + 0,000073 = 0,0029
P = 0,0118 + 0,0179 + 0,0001 + 0,000002 + 0,000002 + 0,000082 = 0,0029
Полученный химический состав стали 30ХМЛ ГОСТ 977-88:
Таблица № 11
С |
Si |
Mn |
Cr |
Mo |
Ni |
S |
P |
0,22 |
0,36 |
0,75 |
0,82 |
0,32 |
0,1 |
0,03 |
0,03 |
6. Технико - экономическое обоснование метода получения заготовки.
В предлагаемой технологии, применения изоляционных вставок в элементах литнково-питающих систем, появляется возможность значительно снижать расходы связанные с плавлением металла и получения годных заготовок. В первую очередь применение вставок позволяет увеличить % выхода годного, тем самым снизить металлоемкость форм. Снизить расход электроэнергии на тонну годных отливок. Если применять изоляционные вставки в качестве прибылей для стального литья, тем самым снижать металлозавалку для плавильных печей это позволит значительно снизить затраты на производство литья. Проводить работу в условиях литейного цеха по внедрению ставок, последовательно, к примеру имея в 30 – 40 наименований со средним % выхода годного 44 % (как к примеру на СЧЛЗ ОАО «Икар») при выпуске 300 тонн в месяц и расхода эл.энергии на тонну 700 кВт. При внедрении в квартал по 10 наименований и увеличения % выхода годного на 10 % можем получить результаты. Рис № 10.
Рис № 10
7. Литература
1. Литейное производство: Учебник для металлургических специальностей вузов. – 2-е изд., перераб. и доп. – М.: Машиностроение, 1987 2. Абрамов Г.Г., Панченко Б.С. Справочник молодого литейщика. – 3- е изд., перераб. и доп. – М.: Высшая школа, 1991 3. Головин С.Я. Справочник литейщика. МАШГИЗ. 4. Климов В.Я., Антонов В.П., Кувыкин Ю.Ф. Проектирование прибылей: Учебное пособие. – Новокузнецк: СибГГМА, 19955. Василевский П.Ф. Технология стального литья. М.: Машиностроение, 19746. ГОСТ 26645-85. Отливки из металлов и сплавов. Допуски размеров, массы и припуски на механическую обработку. – М.: Государственный комитет СССР по стандартам, 19867. ГОСТ 3606-80. Комплекты модельные. Стержневые знаки. Основные размеры. – М.: Государственный комитет СССР по стандартам, 19808. Данные СЧЛЗ ОАО «Икар» Завода трубопроводной арматуры.
9. Данные с интернет сайтов.
Приложение № 1
Комплект
технологической документации.